

We apologize for the inconvenience...
To ensure we keep this website safe, please can you confirm you are a human by ticking the box below.
If you are unable to complete the above request please contact us using the below link, providing a screenshot of your experience.
https://ioppublishing.org/contacts/
Water Jet and Abrasive Water Jet Machining: A Survey of Capability of a Machine in the Field
- Conference: National Conference on Mechanical Engineering Emerging Trends
- At: Vardhman College of Engineering , Hyderabad 501 218 India

- The Maharaja Sayajirao University of Baroda
Abstract and Figures

Discover the world's research
- 25+ million members
- 160+ million publication pages
- 2.3+ billion citations

- V. Viswanatha Chari
- G. Srinivas Kumar

- M. Usha Rani

- J. Mohan Krishna
- R. Muni Sai Preetham

- E. S. Geskin

- J MATER PROCESS TECH

- M. Mazurkiewicz

- Recruit researchers
- Join for free
- Login Email Tip: Most researchers use their institutional email address as their ResearchGate login Password Forgot password? Keep me logged in Log in or Continue with Google Welcome back! Please log in. Email · Hint Tip: Most researchers use their institutional email address as their ResearchGate login Password Forgot password? Keep me logged in Log in or Continue with Google No account? Sign up
Academia.edu no longer supports Internet Explorer.
To browse Academia.edu and the wider internet faster and more securely, please take a few seconds to upgrade your browser .
- We're Hiring!
- Help Center
Abrasive Water Jet Machining
- Most Cited Papers
- Most Downloaded Papers
- Newest Papers
- Unconventional Machine Process Follow Following
- Abrasive Water Jet Maching Follow Following
- Abrasive Waterjet Cutting Follow Following
- Waterjet Cutting Technology Follow Following
- Micro machining Follow Following
- Residual Stresses Follow Following
- Water Jet Follow Following
- Surface integrity Follow Following
- Surface characterization Follow Following
- Abrasive Waterjet Follow Following
Enter the email address you signed up with and we'll email you a reset link.
- Academia.edu Journals
- We're Hiring!
- Help Center
- Find new research papers in:
- Health Sciences
- Earth Sciences
- Cognitive Science
- Mathematics
- Computer Science
- Academia ©2024
Information
- Author Services
Initiatives
You are accessing a machine-readable page. In order to be human-readable, please install an RSS reader.
All articles published by MDPI are made immediately available worldwide under an open access license. No special permission is required to reuse all or part of the article published by MDPI, including figures and tables. For articles published under an open access Creative Common CC BY license, any part of the article may be reused without permission provided that the original article is clearly cited. For more information, please refer to https://www.mdpi.com/openaccess .
Feature papers represent the most advanced research with significant potential for high impact in the field. A Feature Paper should be a substantial original Article that involves several techniques or approaches, provides an outlook for future research directions and describes possible research applications.
Feature papers are submitted upon individual invitation or recommendation by the scientific editors and must receive positive feedback from the reviewers.
Editor’s Choice articles are based on recommendations by the scientific editors of MDPI journals from around the world. Editors select a small number of articles recently published in the journal that they believe will be particularly interesting to readers, or important in the respective research area. The aim is to provide a snapshot of some of the most exciting work published in the various research areas of the journal.
Original Submission Date Received: .
- Active Journals
- Find a Journal
- Proceedings Series
- For Authors
- For Reviewers
- For Editors
- For Librarians
- For Publishers
- For Societies
- For Conference Organizers
- Open Access Policy
- Institutional Open Access Program
- Special Issues Guidelines
- Editorial Process
- Research and Publication Ethics
- Article Processing Charges
- Testimonials
- Preprints.org
- SciProfiles
- Encyclopedia
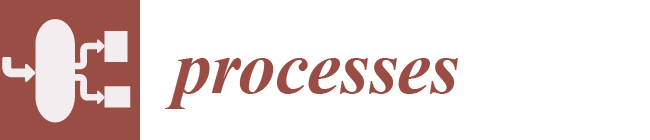
Article Menu
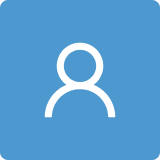
- Subscribe SciFeed
- Recommended Articles
- Google Scholar
- on Google Scholar
- Table of Contents
Find support for a specific problem in the support section of our website.
Please let us know what you think of our products and services.
Visit our dedicated information section to learn more about MDPI.
JSmol Viewer
Computational fluid dynamics analysis of erosion in active components of abrasive water jet machine.
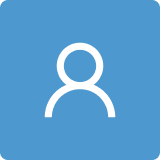
1. Introduction
2. materials and methods, 2.1. granulometry of abrasive material, 2.2. determination of sand particles shape factor, 2.3. determination of abrasive flow rate, 2.4. abrasive fluid modeling by active elements of awj machine, 3. results and discussion, 3.1. results regardint the granulometry of abrasive material, 3.2. determination of sand particles shape factor, 3.3. results regarding the abrasive flow rate, 3.4. results of cfd simulation, 3.4.1. evaluation of the erosion rate (er) produced by particles with 0.19 mm diameter, 3.4.2. evaluation of the er produced by particles with 0.285 mm diameter, 3.4.3. evaluation of the er produced by particles with a diameter of 0.38 mm, 4. conclusions, author contributions, data availability statement, conflicts of interest.
- Patirnac, I.; Ripeanu, R.G.; Laudacescu, E. The Influence of the AWJM Working Parameters on Manufactured Surfaces Microgeometry. MATEC Web Conf. 2020 , 318 , 01011. [ Google Scholar ] [ CrossRef ]
- Baha, V.; Pavlenko, I.; Židek, K.; Ciszak, O. Ensuring the Abrasive Jet Machining Efficiency Using a Nozzle with a Perforated Insert. Machines 2024 , 12 , 347. [ Google Scholar ] [ CrossRef ]
- Baha, V.; Mižáková, J.; Pavlenko, I. An Increase in the Energy Efficiency of Abrasive Jet Equipment Based on the Rational Choice of Nozzle Geometry. Energies 2023 , 16 , 6196. [ Google Scholar ] [ CrossRef ]
- Zou, X.; Fu, L.; Wu, L.; Zuo, W. Research on Multiphase Flow and Nozzle Wear in a High-Pressure Abrasive Water Jet Cutting Head. Machines 2023 , 11 , 614. [ Google Scholar ] [ CrossRef ]
- Patirnac, I.; Ripeanu, R.G.; Ramadan, I.N. Theoretical and Experimental Studies on the Cut Zone Generated by AWJ Process. FME Trans. 2021 , 49 , 997–1004. [ Google Scholar ] [ CrossRef ]
- Iulian Pătîrnac Research on Waterjet Manufacturing of the Metallic Materials Used in Petroleum and Petrochemical Industry ; Petroleum Gas University of Ploiesti: Ploiesti, Romania, 2020.
- Perec, A. Research into the Disintegration of Abrasive Materials in the Abrasive Water Jet Machining Process. Materials 2021 , 14 , 3940. [ Google Scholar ] [ CrossRef ]
- Abrasive Water Jet Machining & Cutting—TechniWaterjet. Available online: https://www.techniwaterjet.com/abrasive-waterjet-machining/ (accessed on 25 August 2024).
- Haldar, B.; Ghara, T.; Ansari, R.; Das, S.; Saha, P. Abrasive Jet System and Its Various Applications in Abrasive Jet Machining, Erosion Testing, Shot-Peening, and Fast Cleaning. Mater. Today Proc. 2018 , 5 , 13061–13068. [ Google Scholar ] [ CrossRef ]
- Anu Kuttan, A.; Rajesh, R.; Dev Anand, M. Abrasive Water Jet Machining Techniques and Parameters: A State of the Art, Open Issue Challenges and Research Directions. J. Braz. Soc. Mech. Sci. Eng. 2021 , 43 , 220. [ Google Scholar ] [ CrossRef ]
- Khan, A.A.; Haque, M.M. Performance of Different Abrasive Materials during Abrasive Water Jet Machining of Glass. J. Mater. Process. Technol. 2007 , 191 , 404–407. [ Google Scholar ] [ CrossRef ]
- Perec, A.; Pude, F.; Grigoryev, A.; Kaufeld, M.; Wegener, K. A Study of Wear on Focusing Tubes Exposed to Corundum-Based Abrasives in the Waterjet Cutting Process. Int. J. Adv. Manuf. Technol. 2019 , 104 , 2415–2427. [ Google Scholar ] [ CrossRef ]
- Cană, P.; Ripeanu, R.G.; Pătîrnac, I.; Diniță, A.; Tănase, M. Investigating the Impact of Operating Conditions on Relief Pressure Valve Flow through CFD and Statistical Analysis. Processes 2023 , 11 , 3396. [ Google Scholar ] [ CrossRef ]
- Pătîrnac, I.; Ripeanu, R.G.; Popescu, C.; Tănase, M. Analysis of Water Flow through the Active Parts of an Abrasive Water Jet Machine: A Combined Analytical and CFD Approach. Processes 2024 , 12 , 1551. [ Google Scholar ] [ CrossRef ]
- Redondo, C.; Chávez–Modena, M.; Manzanero, J.; Rubio, G.; Valero, E.; Gómez–Álvarez, S.; Rivero–Jiménez, A. CFD–Based Erosion and Corrosion Modeling in Pipelines Using a High–Order Discontinuous Galerkin Multiphase Solver. Wear 2021 , 478–479 , 203882. [ Google Scholar ] [ CrossRef ]
- Wang, W.; Sun, Y.; Wang, B.; Dong, M.; Chen, Y. CFD-Based Erosion and Corrosion Modeling of a Pipeline with CO 2 -Containing Gas–Water Two-Phase Flow. Energies 2022 , 15 , 1694. [ Google Scholar ] [ CrossRef ]
- Jafari, M.; Mansoori, Z.; Saffar Avval, M.; Ahmadi, G.; Ebadi, A. Modeling and Numerical Investigation of Erosion Rate for Turbulent Two-Phase Gas–Solid Flow in Horizontal Pipes. Powder Technol. 2014 , 267 , 362–370. [ Google Scholar ] [ CrossRef ]
- Pereira, G.C.; De Souza, F.J.; De Moro Martins, D.A. Numerical Prediction of the Erosion Due to Particles in Elbows. Powder Technol. 2014 , 261 , 105–117. [ Google Scholar ] [ CrossRef ]
- Njobuenwu, D.O.; Fairweather, M. Modelling of Pipe Bend Erosion by Dilute Particle Suspensions. Comput. Chem. Eng. 2012 , 42 , 235–247. [ Google Scholar ] [ CrossRef ]
- Lospa, A.M.; Dudu, C.; Ripeanu, R.G.; Dinita, A. CFD Evaluation of Sand Erosion Wear Rate in Pipe Bends Used in Technological Installations. IOP Conf. Ser. Mater. Sci. Eng. 2019 , 514 , 012009. [ Google Scholar ] [ CrossRef ]
- Ri, J.H.; Ripeanu, R.G.; Dinita, A. Erosion Modeling of Coated Gate Valves. Tribol. Ind. 2022 , 44 , 113–122. [ Google Scholar ] [ CrossRef ]
- Ri, J.; Ripeanu, R.-G.; Dinita, A. Erosion Modeling in Parallel Gate Valve. FME Trans. 2020 , 48 , 808–815. [ Google Scholar ] [ CrossRef ]
- Gandhi, M.B.; Vuthaluru, R.; Vuthaluru, H.; French, D.; Shah, K. CFD Based Prediction of Erosion Rate in Large Scale Wall-Fired Boiler. Appl. Therm. Eng. 2012 , 42 , 90–100. [ Google Scholar ] [ CrossRef ]
- Schüler, M.; Dadgar, M.; Herrig, T.; Bergs, T. Influence of Abrasive Properties on Erosion in Waterjet Machining. Procedia CIRP 2021 , 102 , 375–380. [ Google Scholar ] [ CrossRef ]
- Dhanawade, A.; Wazarkar, S.; Kumar, S. Erosion Model for Abrasive Water Jet Machining of Composite Materials. J. Braz. Soc. Mech. Sci. Eng. 2022 , 44 , 268. [ Google Scholar ] [ CrossRef ]
- Nguyen, T.; Wang, J. A Review on the Erosion Mechanisms in Abrasive Waterjet Micromachining of Brittle Materials. Int. J. Extrem. Manuf. 2019 , 1 , 012006. [ Google Scholar ] [ CrossRef ]
- Kamarudin, N.H.; Prasada Rao, A.K.; Azhari, A. CFD Based Erosion Modelling of Abrasive Waterjet Nozzle Using Discrete Phase Method. IOP Conf. Ser. Mater. Sci. Eng. 2016 , 114 , 012016. [ Google Scholar ] [ CrossRef ]
- Li, L.; Xu, P.; Xu, W.; Lu, B.; Wang, C.; Tan, D. Multi-Field Coupling Vibration Patterns of the Multiphase Sink Vortex and Distortion Recognition Method. Mech. Syst. Signal Process. 2024 , 219 , 111624. [ Google Scholar ] [ CrossRef ]
- Li, L.; Xu, W.; Tan, Y.; Yang, Y.; Yang, J.; Tan, D. Fluid-Induced Vibration Evolution Mechanism of Multiphase Free Sink Vortex and the Multi-Source Vibration Sensing Method. Mech. Syst. Signal Process. 2023 , 189 , 110058. [ Google Scholar ] [ CrossRef ]
- Yin, Z.; Ni, Y.; Li, L.; Wang, T.; Wu, J.; Li, Z.; Tan, D. Numerical Modeling and Experimental Investigation of a Two-Phase Sink Vortex and Its Fluid-Solid Vibration Characteristics. J. Zhejiang Univ. Sci. A 2024 , 25 , 47–62. [ Google Scholar ] [ CrossRef ]
- Mostofa, M.G.; Kil, K.Y.; Hwan, A.J. Computational Fluid Analysis of Abrasive Waterjet Cutting Head. J. Mech. Sci. Technol. 2010 , 24 , 249–252. [ Google Scholar ] [ CrossRef ]
- Deepak, D.; Anjaiah, D.; Karanth, K.V.; Sharma, N.Y. CFD Simulation of Flow in an Abrasive Water Suspension Jet: The Effect of Inlet Operating Pressure and Volume Fraction on Skin Friction and Exit Kinetic Energy. Adv. Mech. Eng. 2012 , 4 , 186430. [ Google Scholar ] [ CrossRef ]
- Pan, Y.; Geng, Z.; Yuan, H.; Zhai, S.; Huo, F. Numerical Simulation and Flow Field Analysis of Porous Water Jet Nozzle Based on Fluent. Appl. Sci. 2024 , 14 , 7075. [ Google Scholar ] [ CrossRef ]
- Ulmanu, V.; Zecheru, G.; Minescu, M.; Săvulescu, M.J. Tehnologia Materialelor. Îndrumar de Laborator ; Institutul de Petrol și Gaze: Ploiești, Romania, 1987. [ Google Scholar ]
- Buzilă, S.; Istrate, G.; Chira, I. Proiectarea Și Executarea Formelor—Lucrări de Laborator Și Aplicații ; Institutul Politehnic București: București, Romania, 1973. [ Google Scholar ]
- ISO 3310-1: 2016 ; Test Sieves-Technical Requirements and Testing—Part 1: Test Sieves of Metal Wire Cloth. ISO: Geneva, Switzerland, 2016.
- STAS 5609-87 ; Nisip Pentru Turnătorie. Contiții Tehnice Generale de Calitate. ASRO: București, Romania, 1987.
- Rodríguez, J.M.; Edeskär, T.; Knutsson, S. Particle Shape Quantities and Measurement Techniques: A Review. Electron. J. Geotech. Eng. 2013 , 18 , 169–198. [ Google Scholar ]
- Lin, J.Z.; Gao, Z.Y.; Zhou, K.; Chan, T.L. Mathematical Modeling of Turbulent Fiber Suspension and Successive Iteration Solution in the Channel Flow. Appl. Math. Model. 2006 , 30 , 1010–1020. [ Google Scholar ] [ CrossRef ]
- Harish, R.; Venkatasubbaiah, K. Mathematical Modeling and Computation of Fire Induced Turbulent Flow in Partial Enclosures. Appl. Math. Model. 2013 , 37 , 9732–9746. [ Google Scholar ] [ CrossRef ]
- Menter, F.R.; Sechner, R.; Matyushenko, A. Best Practice: RANS Turbulence Modeling in Ansys CFD. Available online: https://www.ansys.com/content/dam/amp/2022/february/asset-creation/best-practices-campaign/Best%20Practice-Rans%20turbulence%20modeling%20in%20Ansys%20CFD.pdf (accessed on 16 February 2022).
- Pătîrnac, I.; Ripeanu, R.G.; Laudacescu, E. Abrasive Flow Modelling through Active Parts Water Jet Machine Using CFD Simulation. IOP Conf. Ser. Mater. Sci. Eng. 2020 , 724 , 012001. [ Google Scholar ] [ CrossRef ]
- Ghenaiet, A. Modeling of Particle Trajectory and Erosion of Large Rotor Blades. Int. J. Aerosp. Eng. 2016 , 2016 , 7928347. [ Google Scholar ] [ CrossRef ]
- Rakibuzzaman, M.; Kim, H.-H.; Kim, K.; Suh, S.-H.; Kim, K.Y. Numerical Study of Sediment Erosion Analysis in Francis Turbine. Sustainability 2019 , 11 , 1423. [ Google Scholar ] [ CrossRef ]
- Muttashar, H.L.; Ali, N.B.; Mohd Ariffin, M.A.; Hussin, M.W. Microstructures and Physical Properties of Waste Garnets as a Promising Construction Materials. Case Stud. Constr. Mater. 2018 , 8 , 87–96. [ Google Scholar ] [ CrossRef ]
- Solids-Densities. Available online: https://www.engineeringtoolbox.com/density-solids-d_1265.html (accessed on 25 August 2024).
- Abrasive Garnet Material-Material Safety Data Sheet. Available online: https://gritsablare.ro/docs/fisa-granat-ro.pdf (accessed on 25 August 2024).
- Bonzanini, A.; Picchi, D.; Ferrari, M.; Poesio, P. Velocity Profiles Description and Shape Factors Inclusion in a Hyperbolic, One-Dimensional, Transient Two-Fluid Model for Stratified and Slug Flow Simulations in Pipes. Petroleum 2019 , 5 , 191–198. [ Google Scholar ] [ CrossRef ]
Click here to enlarge figure
- Multiphase flow | ||
- Viscous—SST; k-omega | ||
- Particle material: quartz [ , ]; | ||
- Particle diameter: (190; 285; 380) × 10 m | ||
- Abrasive flow rate: according to , [kg/s] | ||
- Form factor of the particle: 0.62 | ||
- Primary phase: water | ||
- Secondary phase: air | ||
- Abrasive input: | - Speed: 2.542 m/s [ ] | |
- Water inlet: | - Speed: 622.35 m/s [ ] | |
- Exit conditions: | - Pressure: 101,350 Pa [ ] | |
- Time: constant; | ||
- Maximum number of iterations: 50 |
Gradation Machine, x | 0 | 5 | 10 | 15 | 20 |
Abrasive flow rate, Q [g/s] | 3.1807 | 4.8180 | 6.0110 | 6.7580 | 7.0600 |
Property | Density 10 [kg/m ] | Specific Density | Hardness Mohs | Melting Point [°C] |
---|---|---|---|---|
Value | 3.2…4.3 | 3…4 | 7.5…8 | 1250 |
Sieve Number/Mesh Side, [mm] | Granule Size, [mm] | Remain on the Sieve | The Sum of the Cumulative Percentages (Passing through the Sieve) | |
---|---|---|---|---|
[g] | % vs. Working Quantity (50 g) | |||
1 | 0.63–0.1 | 0 | 0 | 100 |
0.8 | 0.4–0.63 | 0 | 0 | 100 |
0.5 | 0.315–0.4 | 0.886 | 1.772 | 98.228 |
0.315 | 0.25–0.315 | 4.7294 | 9.4588 | 88.7692 |
0.25 | 0.16–0.25 | 44.1804 | 88.3608 | 0.4084 |
0.1 | 0.1–0.16 | 0.1972 | 0.3944 | 0.014 |
0.063 | 0.063–0.1 | 0.007 | 0.014 | 0 |
Tray | 0–0.063 | 0 | 0 | 0 |
No. Image Particle | Particle Area, A × 10 [µm ] | Area Circumscribed by the Particle, A × 10 [µm ] | Form Factor, Ψ |
---|---|---|---|
P1 | 0.64917 | 1.10037 | 0.590 |
P2 | 0.46045 | 1.37234 | 0.336 |
P3 | 0.42821 | 0.64071 | 0.668 |
P4 | 0.59066 | 1.35736 | 0.435 |
P5 | 0.38884 | 0.66525 | 0.585 |
P6 | 0.81574 | 1.24621 | 0.655 |
Q7 | 1.04665 | 1.71943 | 0.609 |
P8 | 0.47862 | 0.79153 | 0.605 |
Q9 | 0.88192 | 1.20744 | 0.730 |
P10 | 0.52431 | 0.67682 | 0.775 |
P11 | 0.71004 | 1.07936 | 0.658 |
P12 | 0.74291 | 0.93088 | 0.798 |
Chemical Compound | SiO | Fe O | Al O | MgO | CaO | TiO | P O | MnO |
---|---|---|---|---|---|---|---|---|
Content [%] | 37.20 | 27.80 | 16.60 | 4.70 | 4.95 | 2.5 | 0.05 | 0.5 |
Gradation Machine, x | 0 | 5 | 10 | 15 | 20 |
---|---|---|---|---|---|
Erosion rate, ER (×10 ) [kg/m ·s] | 1.092276 | 1.308244 | 1.493233 | 1.652131 | 2.022878 |
Gradation Machine, x | 0 | 5 | 10 | 15 | 20 |
---|---|---|---|---|---|
Erosion rate, ER (×10 ) [kg/m ·s] | 2.456068 | 2.955192 | 4.456159 | 5.524016 | 6.119593 |
Gradation Machine, x | 0 | 5 | 10 | 15 | 20 |
---|---|---|---|---|---|
Erosion rate, ER (×10 ) [kg/m ·s] | 3.646755 | 5.465438 | 6.715589 | 6.495351 | 7.123866 |
The statements, opinions and data contained in all publications are solely those of the individual author(s) and contributor(s) and not of MDPI and/or the editor(s). MDPI and/or the editor(s) disclaim responsibility for any injury to people or property resulting from any ideas, methods, instructions or products referred to in the content. |
Share and Cite
Pătîrnac, I.; Ripeanu, R.G.; Tănase, M. Computational Fluid Dynamics Analysis of Erosion in Active Components of Abrasive Water Jet Machine. Processes 2024 , 12 , 1860. https://doi.org/10.3390/pr12091860
Pătîrnac I, Ripeanu RG, Tănase M. Computational Fluid Dynamics Analysis of Erosion in Active Components of Abrasive Water Jet Machine. Processes . 2024; 12(9):1860. https://doi.org/10.3390/pr12091860
Pătîrnac, Iulian, Razvan George Ripeanu, and Maria Tănase. 2024. "Computational Fluid Dynamics Analysis of Erosion in Active Components of Abrasive Water Jet Machine" Processes 12, no. 9: 1860. https://doi.org/10.3390/pr12091860
Article Metrics
Article access statistics, further information, mdpi initiatives, follow mdpi.
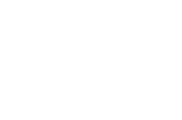
Subscribe to receive issue release notifications and newsletters from MDPI journals
Topography of textured surfaces using an abrasive-water jet technology
- Original Article
- Open access
- Published: 04 September 2024
- Volume 24 , article number 226 , ( 2024 )
Cite this article
You have full access to this open access article
- Monika Szada-Borzyszkowska ORCID: orcid.org/0000-0003-0504-2149 1 ,
- Wojciech Kacalak 1 ,
- Wiesław Szada-Borzyszkowski 2 ,
- Przemysław J. Borkowski 3 ,
- Dorota Laskowska 1 &
- Filip Szafraniec 1
Surface texturing is a technique that allows for the shaping of surface topography to meet various mechanical and tribological requirements. Abrasive-water jet (AWJ) technology is a promising approach to surface texturing, offering minimal heat impact, flexibility, and compatibility with complex surface geometries. High-pressure abrasive-water jet (AWJ) technology, as an innovative and versatile approach, significantly expands the possibilities of surface texturing for materials. Its advantages, such as precision, minimal thermal impact, sustainability, and a wide range of industrial applications, make it an attractive solution across various sectors. With continuous development and integration with modern digital technologies, AWJ is becoming an increasingly practical and cutting-edge tool in surface processing. The abrasive-water jet texturing process also affects surface geometry during the mating of components, which may be significant in reducing wear. The aim of the research was to determine the feasibility of obtaining specific structures on the surface of 304/1.4301 steel using abrasive-water jet technology. Results show that the highest load-bearing ratio of Smrk1 peaks, approximately 25%, was achieved at a texturing speed of 0.803 m/min. Conversely, the lowest load-bearing ratio of Smrk1 peaks, below 10%, was achieved at a texturing speed of 1.948 m/min. Grinding the surface after texturing increases its load-bearing capacity, leading to a twofold increase in the ability to maintain an oil layer. The obtained results may find application in various fields where controlling surface geometry is essential for improving material functionality and efficiency.
Similar content being viewed by others
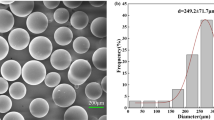
Research on the multilevel energy decrement strategy for abrasive waterjet peening Ti6Al4V
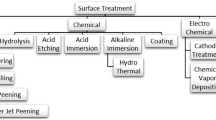
A review on peening processes and its effect on surfaces
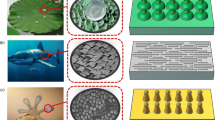
Tribological characteristics and advanced processing methods of textured surfaces: a review
Avoid common mistakes on your manuscript.

1 Introduction
Texturing is a technique of shaping the topography of engineering surfaces to achieve desired mechanical and tribological properties [ 1 ]. It is a process in which patterns or structures are applied to the surfaces of products, aiming to enhance their functionality, durability, or appearance. As a result of surface texturing, it is possible to improve the tribological properties of interacting surfaces, which leads to a reduction in their wear rate [ 2 ]. Surface texture also has a significant impact on the load-bearing capacity, wear resistance, and friction coefficient of tribological components. It is used in the field of engineering due to its advantages in oil lubrication, thermodynamics, hydrodynamics, and aerodynamics [ 3 ].
Surface texturing can also lead to increased corrosion resistance and reduced surface wettability [ 4 ]. In the work by Riveiro et al. [ 5 ], laser texturing is described as a method that changes the surface properties of various materials to control their wettability. It was found that different laser parameters allow for the creation of desired surface structures, which affect the interaction of materials with liquids.
In another study by Shaikh et al. [ 6 ], surface texturing using a femtosecond laser was utilized to treat the surface of 45S5 bioactive glass. Through the application of texturing, a significant reduction in bacterial attachment and biofilm formation was demonstrated, while maintaining biocompatibility with human cells. The results suggest that laser surface modification of 45S5 bioactive glass can effectively impart desired properties to bioimplants and medical devices. In the article by Ijaola et al. [ 7 ], various surface texturing methods were evaluated using techniques such as chemical modification, low-temperature annealing, organic air contaminants, and plasma treatment, necessary to achieve hydrophobicity or superhydrophobicity. The significant potential of laser-textured surfaces was demonstrated for applications such as self-healing surfaces, corrosion resistance, microfluidics, prevention of biological organism settlement, controlling heat flow in systems or materials to maintain proper temperature conditions, and preventing ice formation on the surfaces of various materials or devices.
Moreover, for additional visual effect and increased corrosion protection of metal surfaces, additional coatings are applied [ 8 ]. Surface texturing enhances the adhesion of the coating by increasing the contact surface [ 9 ]. Scientists from France [ 10 ] conducted the application of thermal coatings on textured surfaces. The applied surface texturing increases the adhesion area and the efficiency of particle deposition by appropriately matching the depressions to the particle sizes. The adhesion strength of the coatings significantly increased due to the specific shapes of the patterns, which direct cracks into the interior of the coating, enhancing its adhesion strength. Another group of applications includes adhesive (mechanical) connections in metal–polymer and metal–ceramic composites [ 11 ]. Surface texturing can effectively control bacterial adhesion on biomaterials without antimicrobial agents [ 12 ] or influence cell adhesion [ 13 ], thereby increasing the osseointegration potential of implant surfaces [ 14 ].Textured surfaces find their application in various industries: aerospace, space, civil engineering, renewable energy sector, medical and biotechnology.
Depending on the material and the desired effect, there are several methods for surface texturing. One of the most commonly used methods of surface texturing is laser texturing described earlier [ 15 ], which involves the removal of material through rapid melting or vaporization [ 1 ]. This process has its drawbacks, including the formation of a heat-affected zone and residual stresses in the machined material [ 16 ], which can lead to changes in the metallographic structure, burn marks, microcracks, or delamination [ 17 ]. Another promising method of surface treatment is the utilization of pulsating jet flows [ 18 ]. In the work by Stolárik G. et al., pulsating water jet was employed for roughening surfaces, yielding promising results on titanium samples [ 19 ]. These studies achieved a reduction in surface roughness (Sa and Sz) and a 25.30% increase in subsurface microhardness under specific conditions of linear trajectory and 40 kHz frequency. Moreover, cross trajectory ensures more uniform surfaces, and cross-sectional images revealed potential cell growth sites in the form of microtunnels [ 19 ]. A promising alternative to overcome these limitations while meeting high requirements is texturing using abrasive-water jet (AWJ) technology.
In article [ 20 ], research on creating free-standing structures with high aspect ratios using abrasive-water jet micro-machining is presented. The study employed higher water jet pressures, lower nozzle traverse speeds, and higher abrasive flow rates to minimize structure leveling, resulting in high-quality free-standing structures suitable for radiators. By controlling the depth of micro-abrasive water jet milling, intersecting free-standing microstructures were formed [ 21 ]. The research demonstrated the ability to create deeper intersecting free-standing structures up to 435 μm in height, while maintaining acceptable surface roughness (1.51 μm Ra and 2.47 μm Wa), undercutting (25 μm), and undesirable erosion (3%).
AWJ allows for the elimination of heat influence [ 22 ] or surface oxidation [ 23 ], but it is necessary to provide corrosion protection for the machined surface, especially for materials prone to erosion [ 24 ]. This technology is widely used for cutting various materials, including electrochemical sheet metals used in the construction of transformer cores or parts of electric motor stators and rotors [ 25 ], milling (micronization) [ 26 ], and cleaning surfaces of a wide range of materials [ 27 ].
In abrasive-water jet texturing, material is removed due to the interaction of abrasive particles suspended in a high-pressure water jet expelled from a nozzle. The undeniable advantages of AWJ include the ability to process a wide range of materials, absence of thermal stress generation in the interaction zone, flexibility of the texturing process through changing process parameters, and the ability to process surfaces with complex geometry and precise control of nozzle displacement [ 28 ]. This method, which sustainably utilizes natural resources, is environmentally friendly compared to chemical texturing technology. Textured surfaces can also undergo post-processing, including grinding using grinding wheels [ 29 ] or abrasive films [ 30 ].
While the application of AWJ in surface texturing is gaining increasing interest, this issue is not widely cited in the global literature. In one of the early works, Artaza et al. [ 11 ] described the possibility of using AWJ to ensure a rigid mechanical connection between a textured stainless steel substrate and a glass fiber–epoxy composite. Experimental studies indicated that the parameter with the greatest influence on the roughness of the textured surface was the jet pressure. Banon et al. [ 31 ] utilized AWJ technology for texturing the surface of thin aluminum alloy UNS A92024, analyzing the relationships between process parameters and the roughness of the textured surface. They demonstrated, among other findings, that reducing the displacement velocity results in increased exposure of the abrasive water jet, thereby minimizing kinetic energy losses and reducing the scale of erosion on the textured surface. Continuing their work on texturing thin aluminum alloys, Banon et al. [ 32 ] highlighted that the mass flow rate was a parameter having the greatest influence on surface roughness parameters such as Sa and Sk, as well as surface wettability. Meanwhile, the Sz parameter was mainly defined by the velocity of jet displacement. Special attention should also be paid to the work of Sourd et al. [ 33 ], in which AWJ texturing was used as a surface preparation technique for increasing the adhesive bonding of 3D woven Carbon Fiber Reinforced Polymer (CFRP) substrates. As the research has shown, such an operation led to a change in the mechanical performance of 3D woven CFRP composites. It was found that a higher crater volume correlated with decreased tensile and fatigue performance.
The analysis of surface texturing has shown that this process is significant in many industries, giving materials a unique appearance and texture. Surface texturing enhances the functional properties of materials [ 34 ], such as roughness for better adhesion or wear resistance [ 35 ]. The surface texturing process is crucial in manufacturing, both from aesthetic and functional perspectives. It is a key process that influences the final appearance, functional properties, and value of products [ 36 ].
Filling the gap regarding the application of high-pressure abrasive-water jet surface texturing technology using algorithms to create sophisticated surface structures can bring many benefits and innovations. Utilizing high water pressure and abrasives allows for precise and controlled surface texturing processes [ 37 ]. Complex patterns and textures can be achieved. The ability to control the type of abrasive and the velocity of the jet provides flexibility in achieving various effects [ 38 ]. The process can be tailored to specific needs and requirements for the textured surface. Compared to traditional texturing methods, using abrasive-water jet generates less waste and is more environmentally friendly. The speed and efficiency of the high-pressure abrasive-water jet surface texturing process can contribute to reducing production time and costs. Introducing texturing methods can improve quality, efficiency, and innovation in manufacturing processes.
The work focused on examining the potential use of AWJ jet in the process of developing the surface field structure of processed material using a texture pattern generated by an algorithm.
The aim of the conducted experimental research was to determine the feasibility of obtaining specific structures on the surface of 304/1.4301 steel using abrasive-water jet technology. The conducted studies enabled the determination of the influence of process parameters on the geometry of the produced micro-indentations. The research results form the basis for determining the possibilities of modifying the surface structure using abrasive-water jet technology, allowing for surface adaptation to operate under specific operating conditions.
2 Materials and methods
The high-pressure abrasive-water jet is a versatile tool with various applications. One of these possibilities is its use in surface shaping processes. Its remarkable characteristics minimize the influence of structural changes in the processed material. The basis for selecting the appropriate AWJ texturing parameters was the ability to control the type and amount of abrasive supplied, as well as the jet velocity, providing great flexibility in achieving various effects. This capability was utilized in laboratory studies to achieve diverse surface structures on the processed material.
2.1 Abrasive-water jet surface-texturing equipment
Achieving the appropriate surface structure is an extremely important process from the perspective of its application in subsequent processing stages or usage. Figure 1 shows examples of texture patterns manufactured using high-pressure abrasive-water jet and their topography maps obtained using the confocal microscope LEXT OLS4000 (Olympus, Shinjuku, Tokyo, Japan).
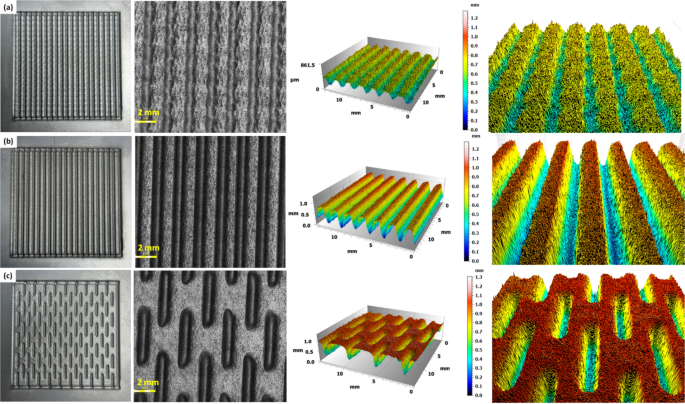
Examples of texture patterns manufactured using high-pressure abrasive-water jet: a texture 1; b texture 2; c texture 3
The structures obtained using AWJ confirmed findings by Ibrahim et al. [ 21 ], demonstrating the capability to produce diverse structures with depths exceeding 400 µm. On the textured surfaces (Fig. 1 ), a clearly directional structure is visible. Depending on the desired results, different depths (Fig. 1 a and b) and shapes (Fig. 1 c) of texturing can be achieved. These properties were utilized in an experimental study of spatially shaping the material surface using AWJ, conducted with an OMAX Jet Machining Center 55,100/4055 (OMAX Corporation, Kent, WA, USA, Fig. 2 ).
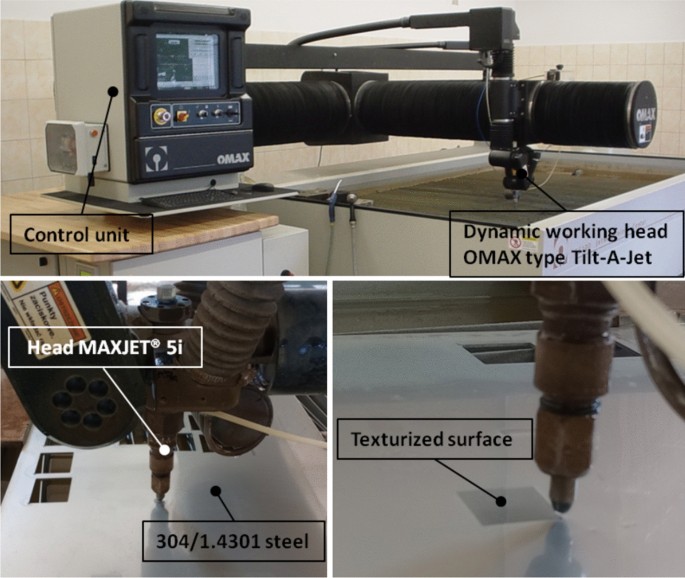
High-pressure abrasive-water jet surface texturing equipment
The OMAX Jet Machining Center is equipped with technical solutions in the form of a high-pressure pump rated at 30 kW. It features a unique Tilt-A-Jet head that dynamically adjusts its angular position relative to the cutting edge. These solutions enable the generation of a high-pressure jet with a maximum pressure of pmax = 385 MPa and a volumetric flow rate of Qmax = 0.065 dm 3 /s. The machine’s cantilever construction ensures high dimensional and shape accuracy, with a deviation value of approximately ± 0.05 mm. The worktable dimensions are 2540 mm by 1400 mm. Surface texturing was carried out under constant parameters as presented in Table 1 .
2.2 Process parameters
OMAX Intelli-ETECH software ((OMAX Corporation, Kent, WA, USA) was used for precising controlling of the AWJ surface texturing process.
In the first stage, the displacement speeds of the working head were determined. The maximum achievable texturing speed is 2.54 m/min. Table 2 presents selected working head speeds for texturing. The textured surfaces had dimensions of 25 mm × 25 mm (chosen for convenient microscopic observations during analysis).
The method involved controlling the displacement speeds of the abrasive-water jet relative to the surface of the textured material, ensuring that the jet interacts with specific areas of the surface at variable time intervals. The result of such variable interaction is varied indentations along the path of the jet's erosion. The general concept is presented in Fig. 3 .
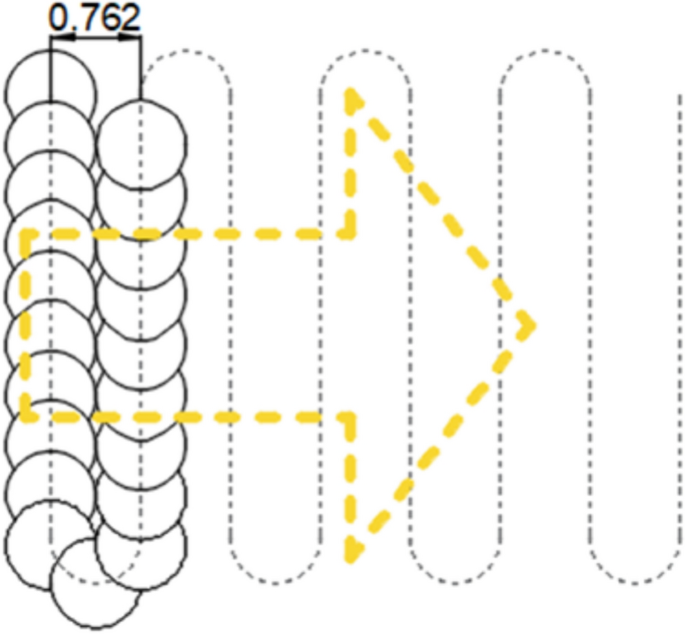
The general concept of AWJ surface texturing process
For the successful implementation of the process, it is necessary to establish the starting and ending points, as well as the orientation of the abrasive-water jet passage. The process was carried out at a pressure of 128 MPa. As a result of subsequent passes of the stream, moved in increments proportional to the diameter of the mixing nozzle opening on the processed material, appropriate cavities were obtained.
For the AWJ surface texturing process, garnet with a granulation of 80 mesh was used as the abrasive. Figure 4 shows the morphology and particle size distribution of the abrasive. Particle size analysis was conducted using a laser particle size analyzer of the Analysette 22 MicroTec Plus type (Fritsch GmbH, Amberg, Germany).
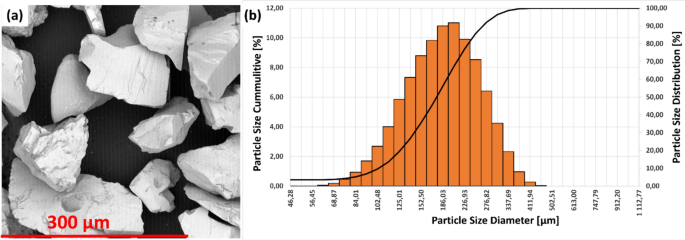
Garnet abrasive used during AWJ surface texturing: a morphology, b particle size distribution of the abrasive used for the texturing process
2.3 Substrate material
The textured substrate was a stainless steel sheet of grade 304/1.4301. The sheet supplier provided relevant certificates. Its basic parameters and chemical composition are presented in Table 3 .
Stainless steel 304/1.4301 is a popular type of material that contains about 18% chromium and 8% nickel. This steel is one of the most commonly used grades of stainless steel due to its good corrosion resistance properties. It is resistant to high temperatures and easy to machine. Stainless steel 304 is used in many fields, such as the food, chemical, and pharmaceutical industries, as well as in the production of kitchenware, fittings, and structural components.
2.4 Examples of surface patterns generated using mathematical algorithm
To generate texture patterns, MATLAB R2024a (Natick, MA, USA) software was used. The texture patterns were generated through operations on data matrices containing information about texture regulation. Examples of generated texture patterns are presented in Fig. 5 .
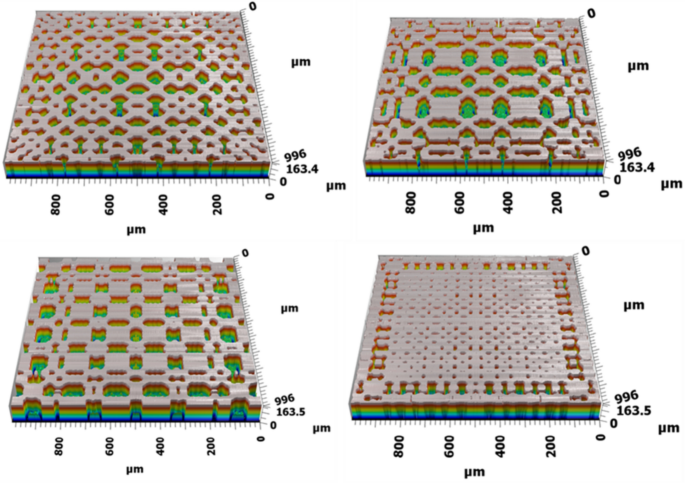
Examples of texture patterns generated with arrangement of straight sections
The generation process involves interactive operations to determine the absolute values from a data vector with a negative harmonic component, followed by multiplying the horizontal and vertical vectors using a convolution operation filter and then smoothing filters. Next, a randomized component typical for abrasive-water jet technology is introduced, and in the final stage, surface elevation modifications are made by mapping the ground surface only on the elevations (Algorithm 1).
The described approach allows for comprehensive utilization of various techniques for generating and visualizing textures patterns. It can also be used to experiment with different types of textures patterns and their modifications in the context of image analysis or computer graphics.
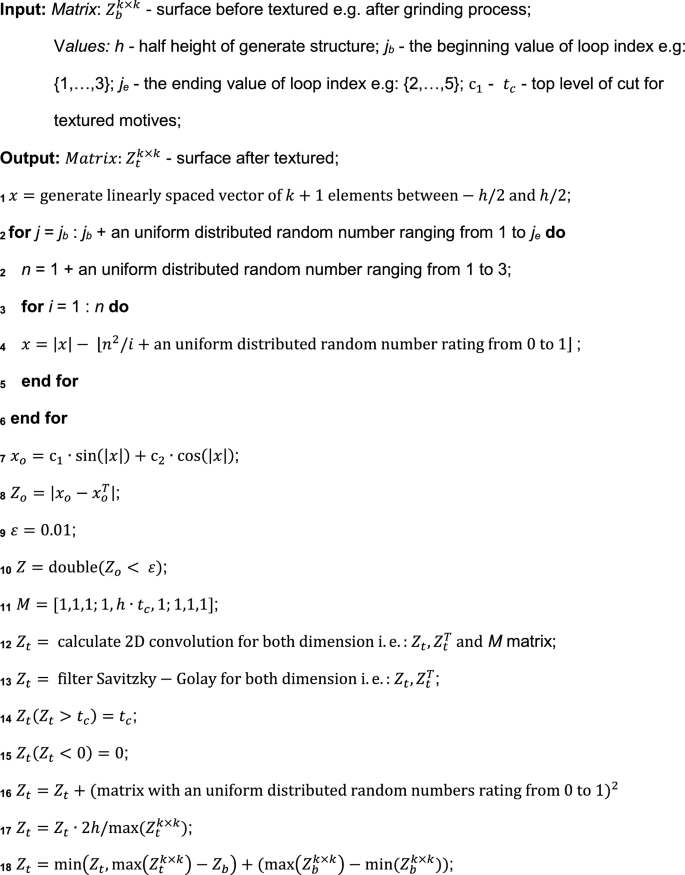
Generate textured surface with arrangement of straight sections
Abrasive-water jet technology offers extensive capabilities for generating various textured structures on material surfaces. Its versatility and precision enable the creation of both microscopic and macroscopic patterns, such as grids, meshes, or hexagons, each with diverse functional properties. Integrated with advanced control systems and capable of combining with other technologies, AWJ becomes an indispensable tool across many industrial sectors.
Example textures generated based on an algorithm are presented in Fig. 6 .
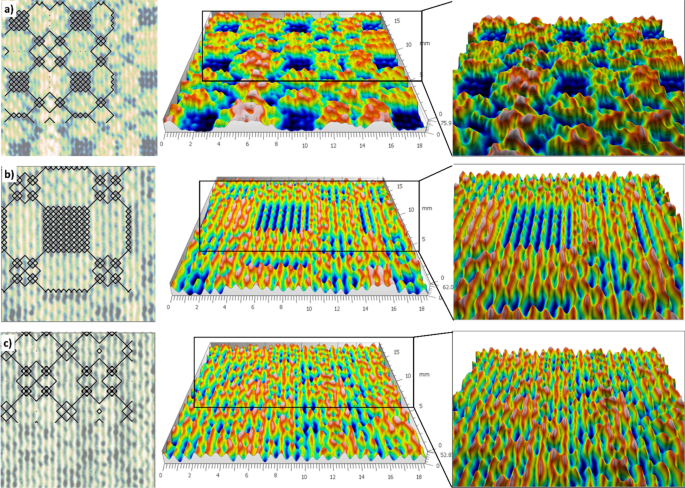
Surface topography of experimentally fabricated structures
2.5 Geometric surface structure and shape deviations analysis
Geometric surface structure analysis for textured surfaces were conducted using the confocal microscope LEXT OLS4000. The basic parameters of microscope are presented in Table 4 .
Thanks to the two operating modes of the LEXT OLS4000 microscope, observations can be carried out non-destructively in both microscope mode and confocal mode. The motorized measurement stage allows for observation and movement in the x–y axes within the observation field, depending on the current magnification, ranging from 16 µm × 16 µm to 2560 µm × 2560 µm.
Measurements were conducted at 108 × magnification. Figure 7 shows the microscope alongside one of the tested samples and the selected area for measurements. The obtained data were analyzed using TalyMap Platinum software (Taylor Hobson, Leicester, UK).
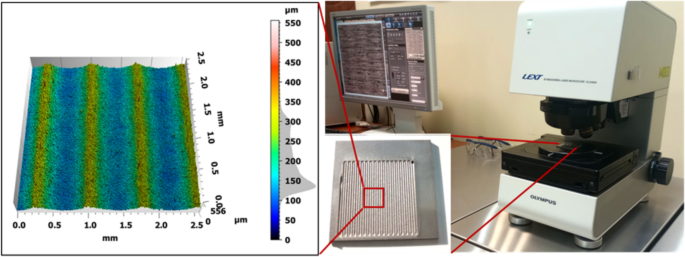
Confocal microscope LEXT OLS4000 with one of the tested samples and the area selected to measurements
3 Results and discussion
3.1 experimental studies on surfaces textured with abrasive-water jet.
The process of shaping textured surfaces with abrasive water jet allowed us to determine the influence of the feed rate of the cutting head on the depths of the indentations (Fig. 8 ).
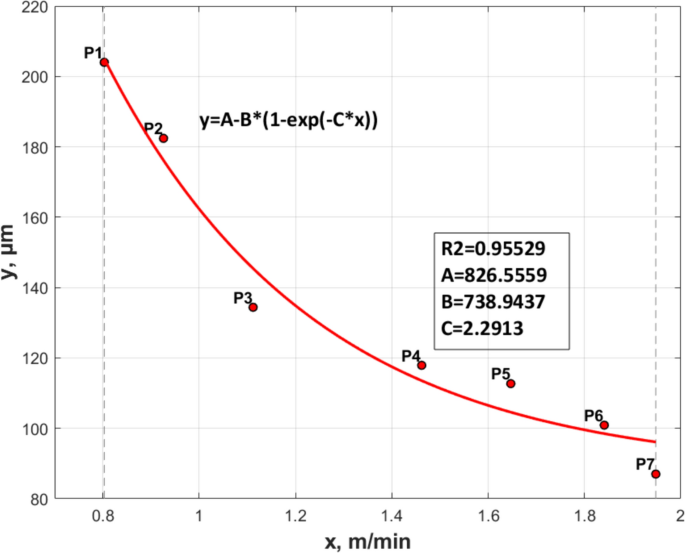
Depth of indentation (y) of the textured surface as a function of the feed rate of the cutting head (x)
To calculate the valley depth of a textured surface as a function of the head displacement speed, a general equation was formulated:
The research results clearly indicate that with an increase in the head displacement speed, the depth of valleys in the textured surface decreases. The valley depth varied depending on the variable displacement speed of the working head, affecting the duration of interaction time between the AWJ and the material. At the lowest investigated speed of 0.803 m/min, the valley depth measured 204 µm. However, at the highest investigated speed of 1.948 m/min, the valley depth decreased to approximately 87 µm (Fig. 8 ).
Based on these results, it was found that increasing the displacement speed of the working head led to a reduction in valley width and an increase in peak width on the tested textured surfaces (Fig. 9 ).
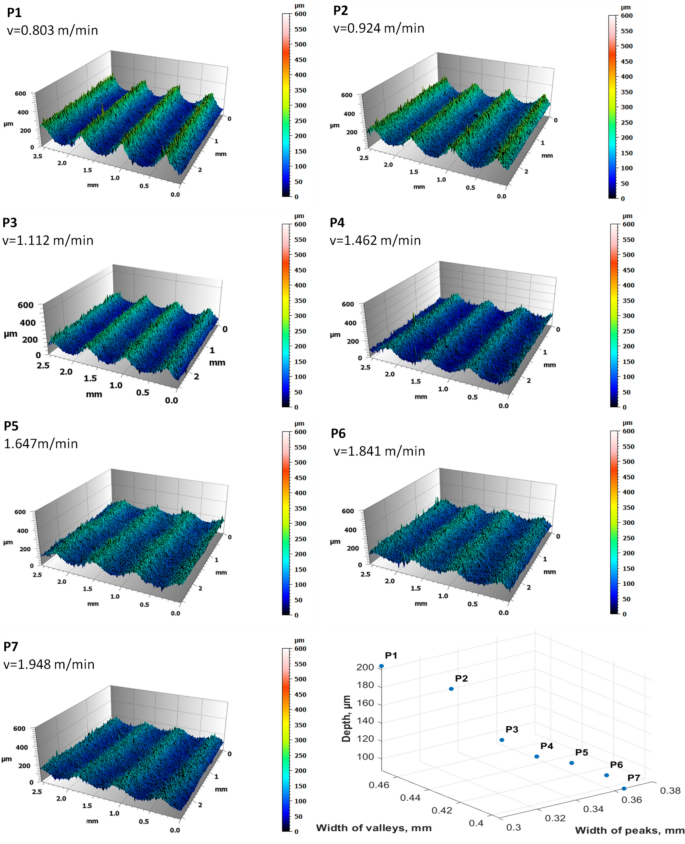
Topography of tested surfaces textured with different displacement speeds of the working head (designations P1–P7 according to Table 2 )
The width of the valleys decreases with increasing displacement speeds of the working head. For the lowest speed of 0.803 m/min, the width of the valleys was 0.47 mm, while for the highest speed of 1.948 m/min, it measured 0.395 mm. Meanwhile, the width of the peaks increases with increasing displacement speeds of the working head, ranging from 0.3 mm at a speed of 0.803 m/min to 0.365 mm at a speed of 1.948 m/min.
In summary, the analysis of the obtained widths of the peaks and valleys revealed a significant dependence on the abrasive water jet processing speed. This property can be utilized to optimize the shaping of the geometric structure of cooperating surfaces, which are exposed to wear or characterized by an increased ability to maintain an oil film.
Friction processes on material surfaces lead to damage or wear, primarily affecting the surface layer of the material. Therefore, the surface formed as a result of texturing with different displacement speeds using abrasive-water jet determines the intensity and course of wear during use. The surface condition, particularly the geometric structure of the surface, is best described by parameters such as surface roughness or structural directionality. The arrangement of peaks and valleys can be described by a bearing curve. The bearing capacity of the analyzed surfaces is presented using Abbott–Firestone curves, as shown in Fig. 10 .
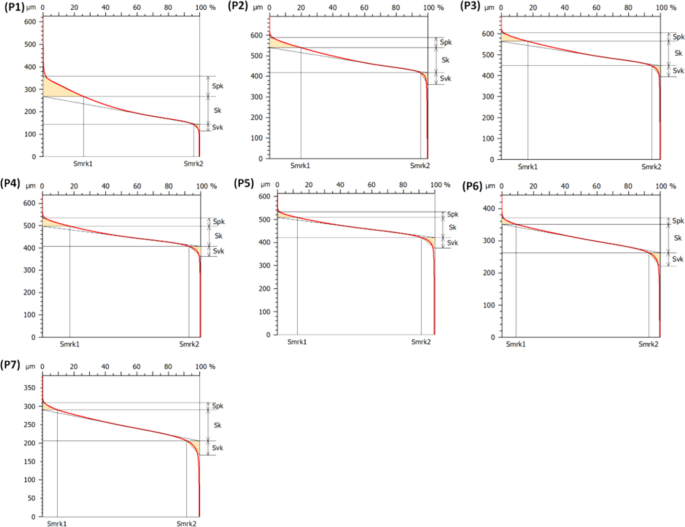
Abbott–Firestone curves for tested surfaces textured with different displacement speeds of the working head (designations P1–P7 according to Table 2 )
The material ratio curves provide reliable information about the shape of the analyzed profiles, including their peaks and valleys. Through appropriate analysis of Abbott-Firestone curves, information about the properties of the analyzed profiles regarding the functional performance of the geometric structure of the surface can be obtained. The observed decrease in the Sk parameter indicates surface smoothing at higher displacement speeds of the working head. Figure 11 presents a group of analyzed parameters upon which an assessment of the functional behavior of the surface after texturing can be based. It has been shown that parameters such as Sa or Sz, depend on the velocity of the AWJ jet, as confirmed by the study of Banon et al. [ 32 ].
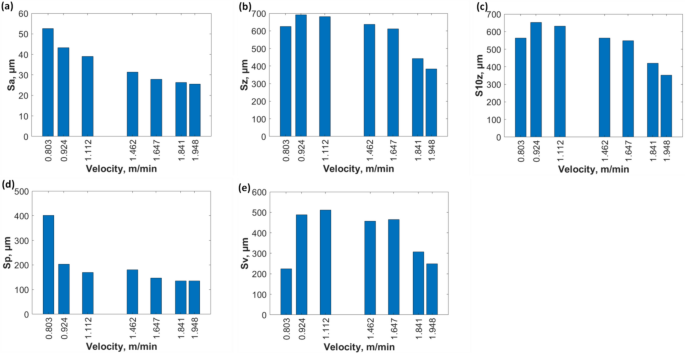
Geometric structure surface parameters for tested AWJ textured surfaces: a Sa—arithmetic mean height, b Sz—maximum height of the surface, c S10z—ten-point height, d Sp—maximum peak height, e Sv—maximum valleys depth
The analysis of the obtained parameter values showed that both the arithmetic mean height of the surface Sa (Fig. 11 a) and its maximum height Sz, and the height of ten-point height S10z (Fig. 11 b and c), decrease with the increase in displacement speeds of working head. For the lowest analyzed displacement speeds, a parameter Sa twice as high was obtained, which is significant in terms of reduced wear resistance of the surface.
The smallest values of the peak height Sp (Fig. 11 d) were obtained for the surfaces textured with speeds of 1.948 m/min (P7), 1.841 m/min (P6) and 1.647 m/min (P5). Therefore, these surfaces have the highest bearing capacity among the analyzed surfaces. The height of the peaks above the core roughness profile Sp determines the behavior of the geometric surface structure during mating of components. Additionally, this is also evidenced by the decreasing load-bearing contribution of the peaks Smrk1 with increasing texturing speed. The highest load-bearing contribution, approximately 25%, of the peaks Smrk1 was obtained for a displacement speed of 0.803 m/min (Fig. 10 , P1). Meanwhile, the lowest load-bearing contribution of the peaks Smrk1, below 10%, was obtained for a texturing speed of 1.948 m/min (Fig. 10 , P7).
The analysis of the depth of the valleys Sv (Fig. 11 e), which is the depth of the valleys located below the core roughness profile, showed similar values for displacement speeds in their middle range and the smallest depths for the lowest and highest speeds. The largest values of the load-bearing contribution of the valleys Smrk2 (Fig. 10 ) were obtained for surfaces textured with moderate displacement speeds. A high value of this parameter indicates the ability to maintain a lubricating oil film held by the surface structure. Surfaces requiring good lubrication should be characterized by large values of Sv parameter.
Figure 12 shows the distribution of surface point frequencies after texturing.
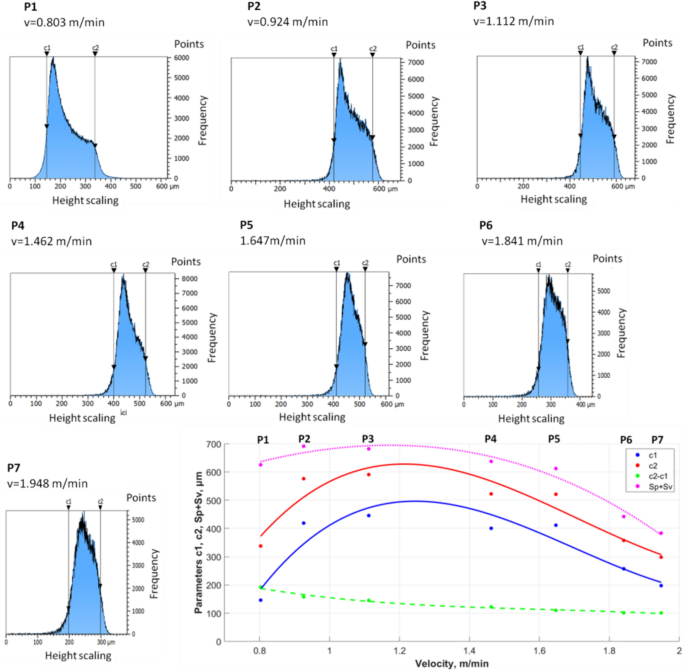
The distribution of surface point heights for tested AWJ textured surfaces (designations P1–P7 according to Table 2 )
The range of frequency distribution decreases with increasing displacement speeds of the working head, indicating surface leveling. The parameter c2-c1 indicates the dispersion of surface point heights. More dispersed surface points can be observed at low displacement speeds of the head. For the lowest speed of 0.803 m/min, this dispersion is 192 µm, whereas for high speeds, it is around 100 µm. Parameters Sp and Sv represent the boundaries of surface point frequencies. The sum (Sp + Sv) of the maximum peak height Sp and the maximum valley depth Sv decreases with increasing displacement speed. Thus, the decrease in this parameter indicates surface smoothing of the textured surfaces at higher speeds.
Table 5 presents the maximum and average depth and density of the valleys for textured surfaces at various displacement speeds of the texturing head.
3.2 Experimental studies of surfaces textured with high-pressure abrasive-water jet after grinding process
Based on the conducted analysis of the textured surface, it was found that the least favorable values of the analyzed geometric surface structure parameters, in terms of the load-bearing contribution of peaks and valleys, were obtained for surfaces P2 and P3, corresponding to low displacement speeds of the working head. To achieve better parameters such as Sp, Sv, Smrk1, and Smrk2 for these surfaces, a grinding process using abrasive films with grit sizes ranging from 14 µm to 20 µm was conducted. Figure 13 shows the surface views of P2 and P3 before and after the grinding process.
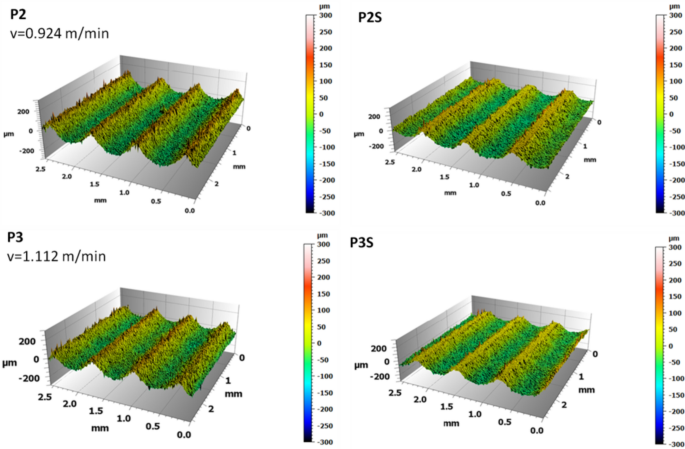
Topography of tested textured surfaces before (P2, P3) and after (P2S, P3S) grinding process using abrasive films
Thanks to the grinding process, the height of the peaks was reduced by 134 µm for P2S and by 89.6 µm for P3S. Figure 14 shows a comparison of Abbott–Firestone curves for selected surfaces before and after smoothing.
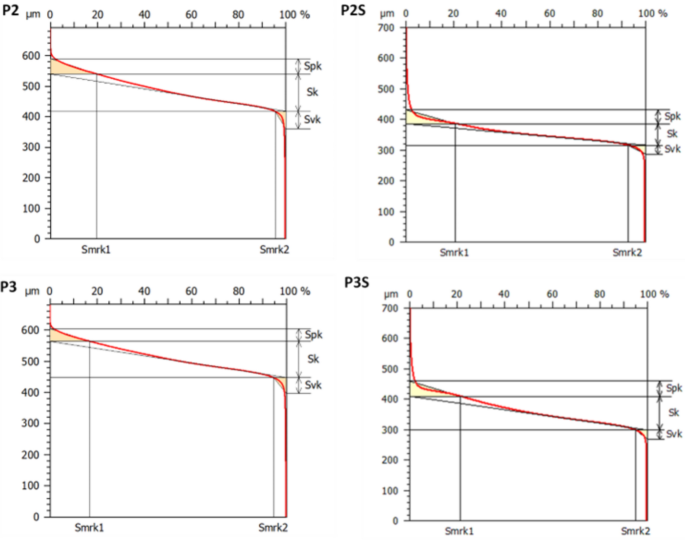
Abbott–Firestone curves for selected surfaces before (P2, P3) and after (P2S, P3S) grinding process
Table 6 presents parameters for quantitative analysis of the load-bearing curve (Abbott–Firestone curves) of the textured surface before and after grinding process.
Based on the obtained load-bearing curve parameters for the textured surface before and after smoothing, a decrease in the Spk parameter was observed, indicating an increase in the load-bearing capacity of these surfaces after grinding by approximately 10% for surface P2S and about 1.5% for surface P3S. A decrease in the Svk parameter by approximately 50% for surfaces after grinding indicates poorer fluid retention by the surface. Figure 15 shows the distribution of surface point heights before and after grinding with abrasive film.
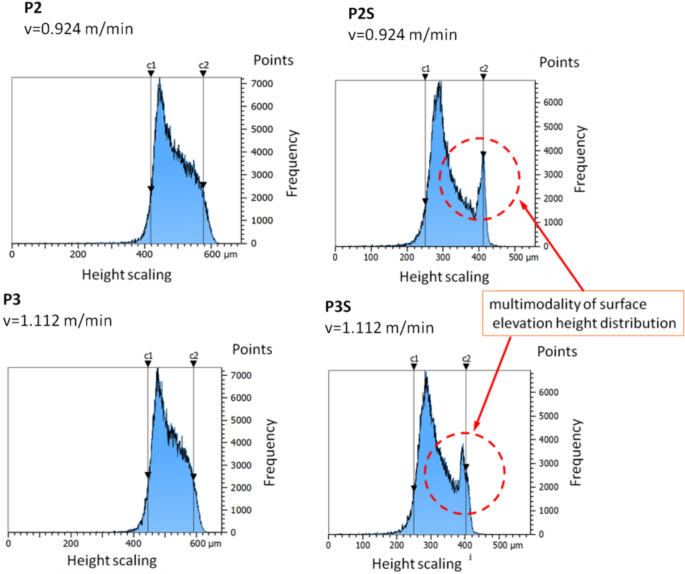
The distribution of surface point heights for selected surfaces before (P2, P3) and after grinding process (P2S, P3S)
The characterization of the elevation distribution of the analyzed surfaces after grinding takes on a bimodal character, indicating the presence of maximum elevation values in two zones. This phenomenon suggests a smoothing effect on the ridges of the textured surfaces.
4 Conclusions
Abrasive-water jet is a tool used in surface treatment processes, especially for metals. Its application for surface texturing can bring several benefits, such as improving coating adhesion, removing scratches, and imparting surface texture. Another aspect advocating for surface structure development is the ability to maintain an oil layer on the surface, which is extremely important in processes requiring surface lubrication. The conducted analysis of the use of AWJ in surface material structuring processes has demonstrated its effectiveness. Based on the conducted research, the following conclusions can be drawn:
The use of AWJ technology for texturing stainless steel surfaces is possible and justified. The results obtained by other researchers [ 32 ] regarding the impact of AWJ texturing speed on the parameters of the geometric surface structure have been confirmed. Increasing the texturing speed increases both surface load-bearing capacity and the ability to maintain an oil film.
The highest load-bearing contribution of peaks, Smrk1 (approximately 25%), was achieved at a texturing speed of 0.803 m/min, while the lowest (below 10%) was observed at a speed of 1.948 m/min.
The surface texturing process has a positive effect on maintaining the geometric structure of the surface during lapping of the elements, causing a decrease in the value of the height of the upper part of the surface Sp and a decrease in the load-bearing share of the Smrk1 vertices with an increase in the texturing speed.
As the texturing speed increases, the depth of the recesses located below the Sv roughness core profile increases and the load-bearing share of the Smrk2 recesses increases, thereby improving the lubricating properties of these surfaces.
The process of grinding the surface after texturing increases the load-bearing capacity of the surface, causing a several percent increase in the Spk parameter, thus doubling the ability of the surface to maintain an oil film.
The use of water abrasive jet in the process of texturing the surface of materials is an innovative technology that offers many advantages over traditional processing methods. Thanks to precise process control and the variety of abrasives used, this technology is not only effective but also sustainable and versatile. Its application in various industries contributes to improving the quality of products and enhancing their aesthetic and functional value. In the implemented surface texturing process, the development of the processed surface was achieved at selected process speeds. New possibilities of controlling the process of shaping the surface processed with an AWJ jet to obtain a surface with the desired functional and operational properties can also be used for other materials. Research on surface texturing of 304/1.4301 steel using abrasive blasting technology (AWJ) has shown that specific surface structures can be obtained, which can significantly improve the functionality and performance of materials in various engineering applications.
Kumar V, Verma R, Kango S, Sharma VS. Recent progresses and applications in laser-based surface texturing systems. Mater Today Commun. 2021;26: 101736. https://doi.org/10.1016/j.mtcomm.2020.101736 .
Article Google Scholar
Mao B, Siddaiah A, Liao Y, Menezes PL. Laser surface texturing and related techniques for enhancing tribological performance of engineering materials: a review. J Manuf Processes. 2020;53:153–73. https://doi.org/10.1016/j.jmapro.2020.02.009 .
Nasir FFM, Ghani JA, Zamri WFHW, Kasim MS. State-of-the-art surface texturing and methods for tribological performance. World Rev Sci Technol Sustain Dev. 2019;15(4):330. https://doi.org/10.1504/WRSTSD.2019.104096 .
Wahab JA, Ghazali MJ, Yusoff WMW, Sajuri Z. Enhancing material performance through laser surface texturing: a review. Trans IMF. 2016;94(4):193–8. https://doi.org/10.1080/00202967.2016.1191141 .
Riveiro A, Pou P, Del Val J, Comesaña R, Arias-González F, Lusquiños F, Boutinguiza M, Quintero F, Badaoui A, Pou J. Laser texturing to control the wettability of materials. Procedia CIRP. 2020;94:879–84. https://doi.org/10.1016/j.procir.2020.09.065 .
Shaikh S, Singh D, Subramanian M, Kedia S, Singh AK, Singh K, Gupta N, Sinha S. Femtosecond laser induced surface modification for prevention of bacterial adhesion on 45S5 bioactive glass. J Non-Cryst Solids. 2018;482:63–72. https://doi.org/10.1016/j.jnoncrysol.2017.12.019 .
Ijaola AO, Bamidele EA, Akisin CJ, Bello IT, Oyatobo AT, Abdulkareem A, Farayibi PK, Asmatulu E. Wettability transition for laser textured surfaces: a comprehensive review. Surf Interfaces. 2020;21: 100802. https://doi.org/10.1016/j.surfin.2020.100802 .
Bagade VU, Duraiselvam M, Sarangi N, Parthiban K. Laser surface texturing to enhance cuniin anti-fretting coating adhesion on Ti6Al4V alloy for aerospace application. Lasers Manuf Mater Process. 2020;7(2):141–53. https://doi.org/10.1007/s40516-020-00114-2 .
Tan N, Xing Z, Wang X, Wang H, Jin G, Xu B. Effects of texturing patterns on the adhesion strength of atmosphere plasma sprayed coatings. J Mater Res. 2017;32(9):1682–92. https://doi.org/10.1557/jmr.2017.164 .
Kromer R, Costil S, Verdy C, Gojon S, Liao H. Laser surface texturing to enhance adhesion bond strength of spray coatings—cold spraying, wire-arc spraying, and atmospheric plasma spraying. Surf Coat Technol. 2018;352:642–53. https://doi.org/10.1016/j.surfcoat.2017.05.007 .
Artaza T, Alberdi A, Olite J, Latapia JL, Gil D, Suarez A, Rivero A. Abrasive waterjet texturing as a method to enhance the embedment of metallic inserts in composite materials. Procedia Eng. 2015;132:724–31. https://doi.org/10.1016/j.proeng.2015.12.553 .
Xu LC, Siedlecki CA. Surface texturing and control of bacterial adhesion. In: Ducheyne P, editor. Comprehensive biomaterials II. Elsevier; 2017. p. 303–20.
Chapter Google Scholar
Shi, B., Fairchild, A., Kleine, Z.; Kuhn, T., Liang, H. Effects of surface texturing on cell adhesion for artificial joints, MRS proceedings 2004, 823, https://doi.org/10.1557/PROC-823-W4.8 .
Shivakoti I, Kibria G, Cep R, Pradhan BB, Sharma A. Laser surface texturing for biomedical applications: a review. Coatings. 2021;11(2):124. https://doi.org/10.3390/coatings11020124 .
Vishnoi M, Kumar P, Murtaza Q. Surface texturing techniques to enhance tribological performance: a review. Surf Interfaces. 2021;27: 101463. https://doi.org/10.1016/j.surfin.2021.101463 .
Martan J, Moskal D, Kučera M. Laser surface texturing with shifted method—functional surfaces at high speed. J Laser Appl. 2019;31(2): 022507. https://doi.org/10.2351/1.5096082 .
Vincent C, Monteil G, Barriere T, Gelin JC. Control of the quality of laser surface texturing. Microsyst Technol. 2008;14(9–11):1553–7. https://doi.org/10.1007/s00542-008-0573-8 .
Szada-Borzyszkowska M, Kacalak W, Banaszek K, Borkowski PJ, Szada-Borzyszkowski W. Analysis of the pulsating properties of a high-pressure water jet generated in a self-excited head for erosion processing. Arch Civ Mech Eng. 2023;23(4):236.
Stolárik G, Svobodová J, Klichová D, Nag A, Hloch S. Titanium surface roughening with ultrasonic pulsating water jet. J Manuf Process. 2023. https://doi.org/10.1016/j.jmapro.2023.02.013 .
Azarsa E, Cinco L, Papini M. Fabrication of high aspect ratio free-standing structures using abrasive water jet micro-machining. J Mater Process Technol. 2020. https://doi.org/10.1016/j.jmatprotec.2019.116318 .
Ibrahim A, Papini M. Controlled depth micro-abrasive waterjet milling of aluminum oxide to fabricate micro-molds containing intersecting free-standing structures. Precision Eng. 2022. https://doi.org/10.1016/j.precisioneng.2022.01.007 .
Lianto JM, Tolouei-Rad M, Vafadar A, Aamir M. recent progress trend on abrasive waterjet cutting of metallic materials: a review. Appl Sci. 2021;11(8):3344. https://doi.org/10.3390/app11083344 .
Natarajan Y, Murugesan PK, Mohan M, Khan SA. Abrasive water jet machining process: a state of art of review. J Manuf Processes. 2020;49:271–322. https://doi.org/10.1016/j.jmapro.2019.11.030 .
Szada-Borzyszkowska ME, Kacalak W, Bohdal Ł, Szada-Borzyszkowski W. Analysis and basics of improving the process of cutting electrical sheet bundles with a high-pressure abrasive water jet. Materials. 2024;17(7):1666. https://doi.org/10.3390/ma17071666 .
Szada-Borzyszkowska M, Kacalak W, Bohdal Ł, Szada-Borzyszkowski W. Analysis of the process and results of high-pressure abrasive water jet multilayer cutting of electrical steel. Materials. 2023;17(1):94. https://doi.org/10.3390/ma17010094 .
Borkowski PJ, Szada-Borzyszkowski W. Micronization of hard coal with the use of a high-pressure water jet. Energies. 2021;14(6):4745. https://doi.org/10.3390/en14164745 .
Khan MA, Soni H, Mashinini P, Uthayakumar M. Abrasive water jet cutting process form machining metals and composites for engineering applications: a review. Eng Res Express. 2021;3(2): 022004. https://doi.org/10.1088/2631-8695/abfe98 .
Wang H, Yuan R, Zhang X, Zai P, Deng J. Research progress in abrasive water jet processing technology. Micromachines. 2023;14(8):1536. https://doi.org/10.3390/mi14081526 .
Lipiński D, Banaszek K, Mathia TG. New methodology for discrimination of topography diversity of engineering surfaces—case of grinding. Measurement. 2022;190: 110659. https://doi.org/10.1016/j.measurement.2021.110659 .
Tandecka K, Kacalak W, Wiliński M, Wieczorowski M, Mathia TG. Superfinishing with abrasive films featuring discontinuous surfaces. Materials. 2024;17(7):1704. https://doi.org/10.3390/ma17071704 .
Bañon, F., Sambruno, A., Gómez, A., Mayuet, P.F. Preliminary study of abrasive water jet texturing on low thickness UNS A92024 alloy sheets. IOP Conf. Ser.: Mater. Sci. Eng. 2021, 1193 (1), 012027, https://doi.org/10.1088/1757-899X/1193/1/012027 .
Bañon F, Sambruno A, Mayuet PF, Gómez-Parra Á. Study of abrasive water jet machining as a texturing operation for thin aluminium alloy UNS A92024. Materials. 2023;16(10):3843. https://doi.org/10.3390/ma16103843 .
Sourd X, Zitoune R, Crouzeix L, Coulaud M. Influence of the texturing quality consecutive to abrasive water jet machining on the adhesive properties in mode I of 3D woven composite assemblies. Compos B. 2022;242: 110091. https://doi.org/10.1016/j.compositesb.2022.110091 .
Baumli P, D’Acunzi M, Hegner KI, Naga A, Wong WSY, Butt HJ, Vollmer D. The challenge of lubricant-replenishment on lubricant-impregnated surfaces. Adv Colloid Interface Sci. 2021. https://doi.org/10.1016/j.cis.2020.102329 .
Maiya PS, Busch DE. Effect of surface fatigue behavior roughness on low-cycle of type 304 stainless steel. Metall Trans A. 1975. https://doi.org/10.1007/BF02642305 .
Naresh Raj KL, Pavithra E. Surface Modification by Abrasive Water Jet Milling of Ti-6Al-4V Alloy for Biomedical Application. In: Sethuraman B, Jain P, Gupta M, editors. Recent advances in mechanical engineering. STAAAR 2022. Lecture notes in mechanical engineering. Singapore: Springer; 2023.
Google Scholar
Husin H, Zaidi N, Gebremariam MA, Azhari A, et al. Effect of masked abrasive waterjet texturing on surface roughness using taguchi method. In: Abdul Sani AS, et al., editors. Enabling industry 4.0 through advances in manufacturing and materials. Lecture notes in mechanical engineering. Singapore: Springer; 2022.
Liu X, Yao L, Li H, et al. AWJ machining of high-volume fraction SiC p /Al composites. Int J Adv Manuf Technol. 2023;129:941–54. https://doi.org/10.1007/s00170-023-12229-9 .
Download references
Scientific work funded from the state budget under the program of the Minister of Science entitled “Polish Metrology II” (Poland), project number PM-II/SP/0038/2024/02, funding amount 999,530.40 PLN, total project value 999,530.40 PLN.
Author information
Authors and affiliations.
Faculty of Mechanical Engineering and Energy, Koszalin University of Technology, Śniadeckich 2, 75-620, Koszalin, Poland
Monika Szada-Borzyszkowska, Wojciech Kacalak, Dorota Laskowska & Filip Szafraniec
Branch of the KUT in Szczecinek, Koszalin University of Technology, 78-400, Szczecinek, Poland
Wiesław Szada-Borzyszkowski
Faculty of Mechanical Engineering, Wroclaw University of Technology, 50-370, Wroclaw, Poland
Przemysław J. Borkowski
You can also search for this author in PubMed Google Scholar
Corresponding author
Correspondence to Monika Szada-Borzyszkowska .
Ethics declarations
Conflict of interest.
All authors declare that they have no conflict of interest.
Ethical approval
This article does not contain any studies with human participants or animals performed by any of the authors.
Additional information
Publisher's note.
Springer Nature remains neutral with regard to jurisdictional claims in published maps and institutional affiliations.
Rights and permissions
Open Access This article is licensed under a Creative Commons Attribution 4.0 International License, which permits use, sharing, adaptation, distribution and reproduction in any medium or format, as long as you give appropriate credit to the original author(s) and the source, provide a link to the Creative Commons licence, and indicate if changes were made. The images or other third party material in this article are included in the article's Creative Commons licence, unless indicated otherwise in a credit line to the material. If material is not included in the article's Creative Commons licence and your intended use is not permitted by statutory regulation or exceeds the permitted use, you will need to obtain permission directly from the copyright holder. To view a copy of this licence, visit http://creativecommons.org/licenses/by/4.0/ .
Reprints and permissions
About this article
Szada-Borzyszkowska, M., Kacalak, W., Szada-Borzyszkowski, W. et al. Topography of textured surfaces using an abrasive-water jet technology. Arch. Civ. Mech. Eng. 24 , 226 (2024). https://doi.org/10.1007/s43452-024-01035-z
Download citation
Received : 10 May 2024
Revised : 17 July 2024
Accepted : 17 August 2024
Published : 04 September 2024
DOI : https://doi.org/10.1007/s43452-024-01035-z
Share this article
Anyone you share the following link with will be able to read this content:
Sorry, a shareable link is not currently available for this article.
Provided by the Springer Nature SharedIt content-sharing initiative
- Abrasive-water jet
- Surface geometry
- Find a journal
- Publish with us
- Track your research

IMAGES
VIDEO
COMMENTS
In AWJ machining, the material is removed by the erosion process, wherein hard abrasive particles are suspended in a high velocity of the water jet stream, which, in turn, increases the acceleration of the abrasive particles, and their kinetic energy impingement towards the target material, causing material removal [3].Fig.1 (c) shows the basic layout of injection type AWJ machining process.
Abrasive water jet machining technology is an unconventional special process technology; its jet stream has high energy, and its machining process is characterized by no thermal deformation, no pollution, high applicability, and high flexibility. It has been widely used for processing different types of materials in different fields. This review elaborates on the basic principles and ...
The abrasive water jet machining (AWJM) process is further established based on various advanced machining techniques by the researchers. ... Finally, this paper addresses open research issues and ...
Introduction. In the 1930s, a low-pressure water jet system was patented and successfully used to cut paper [1].Twenty years later, a high-pressure hydraulic seal from aviation industry was adopted to water jet machining, that noticeably increased the process productivity [2].The continuous increase of working pressure in the next few decades allowed the cutting of hard alloys and carbides.
The abrasive water jet machining (AWJM) process is further established based on various advanced machining techniques by the researchers. ... Finally, this paper addresses open research issues and the potential paths for the future study. References. Chen F, Miao X, Tang Y, Yin S (2017) Review on recent advances in machining methods based on ...
Abrasive water jet machining (AWJM) comes under the mechanical-type nontraditional manufacturing process. In AWJM, a very high water jet pressure is used for the cutting of engineering materials. In AWJM, very high pressure of abrasive laden water in the range of 180-450 MPa is passed through an orifice size of 0.2-0.5 mm diameter [1 ...
Abrasive water jet machining techniques and parameters: a state of the art, open issue challenges and research directions A. Anu Kuttan1 · R. Rajesh2 · M. Dev Anand3 Received: 20 October 2020 / Accepted: 15 February 2021 / Published online: 27 March 2021 ... The review papers were collected from the year 2009 to 2019, and approximately 78 ...
Abrasive water jet machining is an extended version of water jet machining where abrasive particles such as aluminum oxide, silicon carbide , or garnet are contained within the water jet with the purpose of raising the rate of material removal beyond that of a water jet machine [3, 4].Abrasive water jet machining process can be employed to a wide range of materials that are soft from rubbers ...
The cutting action of abrasive water jet machining is performed by the mechanical impact of tiny abrasives as noncountable cutting edges alongside the impact energy of an extreme-pressure water jet. Brass is an alloy of copper and zinc, known for its high electrical and thermal conductivity as well as durability and reliability.
Jayakumar K. Abrasive water jet machining studies on Kenaf/E-glass fiber polymer composite. Proceedings of 10th international conference on precision, meso, micro and nano engineering 2017; 396-399.
Abrasive water-jet machining (AWJM) is an excellent technology for the simultaneous machining of both materials. However, defects at the micro and macro-geometric level have been detected in several scientific articles. ... Feature papers represent the most advanced research with significant potential for high impact in the field. A Feature ...
From the macroscopic point of view, jet working pressure P, traverse rate of nozzle V t r a v, stand-off distance (SOD) H and mass flow rate can affect the quality of kerf profiles and the machining effect. Azmir et al. (2007) and Pal and Choudhury (2014) documented that with increased jet working pressure P, the abrasive kinetic energy in the jet increases, cutting depth and material removal ...
The paper presents aspects regarding an innovative nonconventional technology, abrasive water jet machining. The study also presents results regarding other technological operations possible to be ...
Waterjet machining has attracted great attention in the conditions of hard-to-machine materials, microstructures, or complicated industrial components, and it has become well-established in all major areas of theoretical researches and already been found across the broad spectrum of technical application areas especially in the specific sectors of scientific frontiers, including the mechanical ...
This paper reports some results of experimental investigation conducted on abrasive water jet machining (AWJM) of medium carbon low alloy (EN24) steel. EN24 steel samples of different thickness have been machined at various combinations of AWJM parameters.
The paper presents aspects regarding an innovative nonconventional technology, abrasive water jet machining. The study also presents results regarding other technological operations possible to be ...
Abrasive water jet (AWJ) has been widely used in the development of reservoir resources. In the relevant literature, the mechanism of perforation formation by AWJ impacting rocks in different reservoirs, the effect of rock genesis and mineral species during the material removal process, and the location of crack propagation remain unclear, and there is no comprehensive study that investigates ...
Abstract. Abrasive water jet (AWJ) machining is one of the best non-conventional machining processes, which is being used in modern industries. Operations like cutting, polishing, deburring etc. are often done successfully with the help of AWJ machining processes. This paper reviews the latest techniques being applied in this machining and also ...
This paper presents research work involved in abrasive water jet machining of carbon epoxy composite material. Four process parameters, namely pressure, traverse rate, stand-off distance and abrasive mass flow rate, are considered for this study. Response surface methodology is used to design the experiments.
This paper reviews the Abrasive Water Jet Machining (AWJM) process and capability of an existing CNC Abrasive Water Jet (AWJ) Machine, installed and being used in the field for machining of metals ...
Both cutting conditions were investigated by varying the water jet pressure, the abrasive mesh size and the abrasive water jet impact angle. Optical microscopy and Scanning Electron Microscope with Energy Dispersive X-ray Spectroscopy was used for studying the micro structure and morphology of the cut surfaces under both cutting conditions.
The abrasive water jet machine technology represents a relatively new, emerging non-conventional way of cutting almost all sorts of materials and shapes. The research tendency in abrasive water jet machining fields was approximately counted based on the engineering village database in recent years as shown in Fig. 1. Though this trend has a ...
Abrasive water jet machining (AWJM) is proved to be an efficient and economical process for machining of composites in manufacturing industries. ... In this paper, the published literature during the last three decades (1991-2020) in the domain of AWJM of composites is reviewed. ... M. M. Korat and G. D. Acharya, A review on current research ...
This study presents a comprehensive three-dimensional computational fluid dynamics (CFD) analysis of abrasive fluid flow and its erosive effects on the active components of the WUXI YCWJ-380-1520 water jet cutting machine. The research investigates the behavior and impact of abrasive particles within the fluid, determining the erosion rates for particles with diameters of 0.19 mm, 0.285 mm ...
The abrasive-water jet texturing process also affects surface geometry during the mating of components, which may be significant in reducing wear. The aim of the research was to determine the feasibility of obtaining specific structures on the surface of 304/1.4301 steel using abrasive-water jet technology.