To read this content please select one of the options below:
Please note you do not have access to teaching notes, critical parameters influencing the quality of metal castings: a systematic literature review.
International Journal of Quality & Reliability Management
ISSN : 0265-671X
Article publication date: 26 October 2021
Issue publication date: 17 January 2023
Casting is one of the well-known manufacturing processes to make durable parts of goods and machinery. However, the quality of the casting parts depends on the proper choice of process variables related to properties of the materials used in making a mold and the product itself; hence, variables related to product/process designs are taken into consideration. Understanding casting techniques considering significant process variables is critical to achieving better quality castings and helps to improve the productivity of the casting processes. This study aims to understand the computational models developed for achieving better quality castings using various casting techniques.

Design/methodology/approach
A systematic literature review is conducted in the field of casting considering the period 2000–2020. The keyword co-occurrence network and word cloud from the bibliometric analysis and text mining of the articles reveal that optimization and simulation models are extensively developed for various casting techniques, including sand casting, investment casting, die casting and squeeze casting, to improve quality aspects of the casting's product. This study further investigates the optimization and simulation models and has identified various process variables involved in each casting technique that are significantly affecting the outcomes of the processes in terms of defects, mechanical properties, yield, dimensional accuracy and emissions.
This study has drawn out the need for developing smart casting environments with data-driven modeling that will enable dynamic fine-tuning of the casting processes and help in achieving desired outcomes in today's competitive markets. This study highlights the possible technology interventions across the metal casting processes, which can further enhance the quality of the metal casting products and productivity of the casting processes, which show the future scope of this field.
Research limitations/implications
This paper investigates the body of literature on the contributions of various researchers in producing high-quality casting parts and performs bibliometric analysis on the articles. However, research articles from high-quality journals are considered for the literature analysis in identifying the critical parameters influencing quality of metal castings.
Originality/value
The systematic literature review reveals the analytical models developed using simulation and optimization techniques and the important quality characteristics of the casting products. Further, the study also explores critical influencing parameters involved in every casting process that significantly affects the quality characteristics of the metal castings.
- Optimization
- Bibliometric analysis
Suthar, J. , Persis, J. and Gupta, R. (2023), "Critical parameters influencing the quality of metal castings: a systematic literature review", International Journal of Quality & Reliability Management , Vol. 40 No. 1, pp. 53-82. https://doi.org/10.1108/IJQRM-11-2020-0368
Emerald Publishing Limited
Copyright © 2021, Emerald Publishing Limited
Related articles
All feedback is valuable.
Please share your general feedback
Report an issue or find answers to frequently asked questions
Contact Customer Support

- What is Context Architecture
- Consumer Research
- Behavioural Interventions
- Case Studies
We are 1001 stories.

So are you.
Because that’s how we make sense of the world we live in. Through stories. Written by us, co-authored by our context
1001 is a user-consumer influence & interventions consultancy. We use Context Architecture™ and Behavioural Science to analyse, understand and channel intuitive human behaviour towards creating better products, brands and people.
What is Context Architecture?
Human behaviour is nothing but reaction to context.
User & Consumer Research

From thoughtful buying behaviour to non-conscious triggers, 1001 Stories’ in-depth multi-disciplinary methods will uncover your user/consumers’ strongest impulses, instincts and contextual associations.
We help you understand and put into perspective, the often contrarian behaviours of your customers.
Behavioural Interventions & Business Solutions

Products, brands and companies are aiming to evolve and create quicker, habit-friendlier user paths. We must, then, innovate for human instinct, not challenge it. Don’t make them think. Think for them.
We evaluate user and consumer journeys to identify macro and micro paths in their decision making. This helps us create behaviourally informed brands, products and interventions.
What Our Clients Say
“These guys are our secret sauce.”
Founder, Scaler Academy
1001 Stories is a polymorphic disciple of many schools. We are a team of behavioural science strategists, data scientists, anthropologists, ethnographers, context architects, brand strategists and designers who ask annoying questions like why do we follow superstition more stringently than traffic rules? Can primitive gestures and the reduced motor skills of infants help us create superior gesture driven technology? And what do changing home and architecture trends tell us about the journey of women in society?

Prakash sharma
Behavioural Strategist, Co-Founder of 1001 Stories

reshma tonse
Context Architect, Co-Founder of 1001 Stories
Write to Us
- [email protected] +91-99867 11169

Casting and Casting Processes
39 Pages Posted: 12 Jul 2017
D. G. Mahto
Green Hills Engineering College
Date Written: March 10, 2015
The casting process was discovered probably around 3500 BC in Mesopotamia. Casting is unique manufacturing processes for a variety of reasons. Perhaps the most obvious is the array of molding and casting processes available that are capable of producing complex components in any metal, ranging in weight from less than an ounce to single parts weighing several hundred tons. Foundry processes are available and in use that are economically viable for producing a single prototype part, while others achieve their economies in creating millions of the same part. Virtually any metal that can be melted can and is being cast. Many parts and components are made by casting, including automotive components such as carburettors, engine blocks, crankshafts, agricultural and rail road equipments, pipe and pumping fixtures, power tools, gun barrels and large components of hydraulic turbines etc. Since 1950, partially automated casting processes have been developed for production lines.It is estimated that castings are used in 90% or more of all manufactured goods and in all capital goods machinery used in manufacturing. The diversity in the end use of metal castings is a direct result of the many functional advantages and economic benefits that castings offer compared to other metal forming methods. The beneficial characteristics of a cast component are directly attributable to the inherent versatility of the casting process.
Suggested Citation: Suggested Citation
Dalgobind Mahto (Contact Author)
Green hills engineering college ( email ).
SP-43, RIICO Industrial Area Kukas Jaipur, Rajasthan 302028 India 8058799995 (Phone) 8058799995 (Fax)
Do you have a job opening that you would like to promote on SSRN?
Paper statistics, related ejournals, simulation ejournal.
Subscribe to this fee journal for more curated articles on this topic
Operations Management eJournal
Technology, operations management & production ejournal, facility design ejournal, industrial & manufacturing engineering ejournal, materials engineering ejournal, materials science ejournal, materials performance ejournal, materials processing & manufacturing ejournal.
Information
- Author Services
Initiatives
You are accessing a machine-readable page. In order to be human-readable, please install an RSS reader.
All articles published by MDPI are made immediately available worldwide under an open access license. No special permission is required to reuse all or part of the article published by MDPI, including figures and tables. For articles published under an open access Creative Common CC BY license, any part of the article may be reused without permission provided that the original article is clearly cited. For more information, please refer to https://www.mdpi.com/openaccess .
Feature papers represent the most advanced research with significant potential for high impact in the field. A Feature Paper should be a substantial original Article that involves several techniques or approaches, provides an outlook for future research directions and describes possible research applications.
Feature papers are submitted upon individual invitation or recommendation by the scientific editors and must receive positive feedback from the reviewers.
Editor’s Choice articles are based on recommendations by the scientific editors of MDPI journals from around the world. Editors select a small number of articles recently published in the journal that they believe will be particularly interesting to readers, or important in the respective research area. The aim is to provide a snapshot of some of the most exciting work published in the various research areas of the journal.
Original Submission Date Received: .
- Active Journals
- Find a Journal
- Proceedings Series
- For Authors
- For Reviewers
- For Editors
- For Librarians
- For Publishers
- For Societies
- For Conference Organizers
- Open Access Policy
- Institutional Open Access Program
- Special Issues Guidelines
- Editorial Process
- Research and Publication Ethics
- Article Processing Charges
- Testimonials
- Preprints.org
- SciProfiles
- Encyclopedia
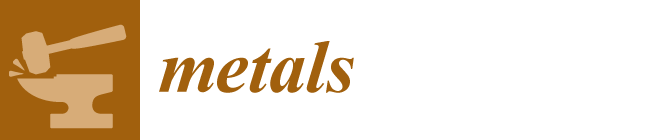
Article Menu
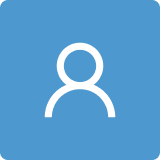
- Subscribe SciFeed
- Recommended Articles
- Google Scholar
- on Google Scholar
- Table of Contents
Find support for a specific problem in the support section of our website.
Please let us know what you think of our products and services.
Visit our dedicated information section to learn more about MDPI.
JSmol Viewer
Continuous casting preparation process of helical fiber-reinforced metal matrix composites.
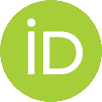
1. Introduction
2. experimental section, 2.1. design and manufacturing of experimental equipment, 2.2. material, 2.3. process parameters, 2.4. testing, 2.4.1. the shape of helical carbon fiber in composites, 2.4.2. interface and mechanical property of helical carbon fiber-reinforced aluminum composites, 3.1. coordinate system, 3.2. basic assumptions, 3.3. the formation processing of helical fiber, 3.3.1. initial state, 3.3.2. transition state, 3.3.3. stable state, 3.4. the angle θ a b difference between point a and point b, 4. results and discussion, 4.1. shape stability of helical carbon fiber in lead matrix, 4.2. influence of process parameters on the shape of helical carbon fiber in lead matrix, 4.2.1. melting temperature, 4.2.2. cooling intensity, 4.2.3. carbon fiber rotation speed, 4.3. prediction of the helical fiber shape, 4.4. helical carbon fiber-reinforced aluminum matrix composites, 4.4.1. the shape of helical carbon fiber, 4.4.2. interface of carbon fiber and aluminum matrix, 4.4.3. mechanical properties, 5. conclusions, author contributions, data availability statement, conflicts of interest.
- Sharma, D.K.; Mahant, D.; Upadhyay, G. Manufacturing of metal matrix composites: A state of review. Mater. Today Proc. 2020 , 26 , 506–519. [ Google Scholar ] [ CrossRef ]
- Shirvanimoghaddam, K.; Hamim, S.U.; Karbalaei Akbari, M.; Fakhrhoseini, S.M.; Khayyam, H.; Pakseresht, A.H.; Ghasali, E.; Zabet, M.; Munir, K.S.; Jia, S.; et al. Carbon fiber reinforced metal matrix composites: Fabrication processes and properties. Compos. Part A Appl. Sci. Manuf. 2017 , 92 , 70–96. [ Google Scholar ] [ CrossRef ]
- Daoud, A. Microstructure and tensile properties of 2014 Al alloy reinforced with continuous carbon fibers manufactured by gas pressure infiltration. Mater. Sci. Eng. A 2005 , 391 , 114–120. [ Google Scholar ] [ CrossRef ]
- Yang, Q.; Liu, J.; Li, S.; Wang, F.; Wu, T. Fabrication and mechanical properties of Cu-coated woven carbon fibers reinforced aluminum alloy composite. Mater. Des. 2014 , 57 , 442–448. [ Google Scholar ] [ CrossRef ]
- Rong, X.; Zhao, D.; He, C.; Zhao, N. Review: Recent progress in aluminum matrix composites reinforced by in situ oxide ceramics. J. Mater. Sci. 2024 , 59 , 9657–9684. [ Google Scholar ] [ CrossRef ]
- Kumar, A.; Singh, V.P.; Singh, R.C.; Chaudhary, R.; Kumar, D.; Mourad, A.-H.I. A review of aluminum metal matrix composites: Fabrication route, reinforcements, microstructural, mechanical, and corrosion properties. J. Mater. Sci. 2024 , 59 , 2644–2711. [ Google Scholar ] [ CrossRef ]
- Li, S.; Fu, S.; Zhou, B.; Zeng, Q. Bamboo—A natural bio-composite research. J. Mater. Res. 1994 , 8 , 188–192. [ Google Scholar ]
- Li, S.; Zhou, B.; Zhen, Z.; Zeng, Q. A biomimetic composite model at the mesoscale. Adv. Mater. Sci. 1991 , 5 , 543–547. [ Google Scholar ]
- Meyers, M.A.; Chen, P.Y.; Lin, A.Y.M.; Seki, Y. Biological materials: Structure and mechanical properties. Prog. Mater. Sci. 2008 , 53 , 1–206. [ Google Scholar ] [ CrossRef ]
- Shao, Y.; Zhao, H.P.; Feng, X.Q.; Gao, H. Discontinuous crack-bridging model for fracture toughness analysis of nacre. J. Mech. Phys. Solids 2012 , 60 , 1400–1419. [ Google Scholar ] [ CrossRef ]
- Ji, B.; Gao, H. Mechanical principles of biological nanocomposites. Annu. Rev. Mater. Res. 2010 , 40 , 77–100. [ Google Scholar ] [ CrossRef ]
- Reese, S.P.; Maas, S.A.; Weiss, J.A. Micromechanical models of helical superstructures in ligament and tendon fibers predict large Poisson’s ratios. J. Biomech. 2010 , 43 , 1394–1400. [ Google Scholar ] [ CrossRef ] [ PubMed ]
- Grason, G.M. Braided bundles and compact coils: The structure and thermodynamics of hexagonally packed chiral filament assemblies. Phys. Rev. E 2009 , 79 , 041919. [ Google Scholar ] [ CrossRef ] [ PubMed ]
- Li, L.; Weaver, J.C.; Ortiz, C. Hierarchical structural design for fracture resistance in the shell of the pteropod Clio pyramidata. Nat. Commun. 2015 , 6 , 6216. [ Google Scholar ] [ CrossRef ] [ PubMed ]
- Zhao, Z.; Li, B.; Feng, X. Handedness-dependent hyperelasticity of biological soft fibers with multilayered helical structures. Int. J. Non-Linear Mech. 2016 , 81 , 19–29. [ Google Scholar ] [ CrossRef ]
- Li, S.; Zhang, R.; Fu, S.; Chen, X.; Zhou, B. A Biomimetic Model of Fiber-reinforced Composite Materials. J. Mater. Sci. Technol. 1994 , 10 , 34–38. [ Google Scholar ]
- Li, S.; Fu, S.; Zhou, B.; Zeng, Q. Experimental investigation of biomimetic double-helical reinforcing elements. J. Mater. Sci. Lett. 1995 , 14 , 769–772. [ Google Scholar ] [ CrossRef ]
- Kagawa, Y.; Nakata, E.; Yoshida, S. Fracture Toughness of Helical Fiber Reinforced Cu/W Composites. J. Japan Inst. Met. 1983 , 47 , 760–767. [ Google Scholar ] [ CrossRef ]
- Wang, L.; Cui, Y.; Qin, Q.; Wang, H.; Wang, J. Helical Fiber Pull-out in Biological Materials. Acta Mech. Solida Sin. 2016 , 29 , 243–255. [ Google Scholar ] [ CrossRef ]
- Wang, L.; Yuan, L.; Wang, L.; Cui, Y.; Qin, Q. Numerical Study on Helical Fiber Fragmentation in Chiral Biological Materials. Trans. Tianjin Univ. 2018 , 24 , 51–58. [ Google Scholar ] [ CrossRef ]
- Liu, S.; Chen, Y.; Zhu, Z.; Ren, E.; Wang, J.; Wang, Y.; Qin, J.; Cheng, P. Bioinspired helical fiber/elastomer composites with high strength. Polymer 2024 , 302 , 127072. [ Google Scholar ] [ CrossRef ]
- Chang, X.; Xu, Q.; Lv, J.; Xu, L.; Zhu, Z.; Liu, S.; Liu, X.; Qin, J. Bioinspired 3D helical fibers toughened thermosetting composites. Compos. Part B Eng. 2021 , 216 , 108855. [ Google Scholar ] [ CrossRef ]
- Liang, J.; Wu, C.; Zhao, Z.; Tang, W. Forming Process and Simulation Analysis of Helical Carbon Fiber Reinforced Aluminum Matrix Composite. Metals 2021 , 11 , 2024. [ Google Scholar ] [ CrossRef ]
- Slepyan, L.I.; Krylov, V.I.; Parnes, R. Helical inclusion in an elastic matrix. J. Mech. Phys. Solids 2000 , 48 , 827–865. [ Google Scholar ] [ CrossRef ]
- Gao, Y.; Li, B.; Wang, J.; Feng, X.-Q. Fracture toughness analysis of helical fiber reinforced biocomposites. J. Mech. Phys. Solids 2021 , 146 , 104206. [ Google Scholar ] [ CrossRef ]
- GB/T228.1-2021 ; Metallic Materials-Tensile Testing-Part 1: Method of Test at Room Temperature. Standardization Administration of the People’s Republic of China: Beijing, China, 2021.
Click here to enlarge figure
Fiber Diameter | Strength (GPa) | Modulus (GPa) | Elongation (%) | Density ) |
---|---|---|---|---|
7 | 3.5 | 230 | 1.5 | 1.78 |
Parameters | Range | |
---|---|---|
Lead Matrix | Aluminum Matrix | |
Carbon fiber rotation speed | 0.67, 1.33 | 0.67 |
Carbon rotation radius | 7.0 | 7.0 |
Melt temperature | 490, 500, 510, 520 | 780 |
Cooling intensity | 350, 450 | 450 |
Continuous casting speed | 5.5 | 5.5 |
The statements, opinions and data contained in all publications are solely those of the individual author(s) and contributor(s) and not of MDPI and/or the editor(s). MDPI and/or the editor(s) disclaim responsibility for any injury to people or property resulting from any ideas, methods, instructions or products referred to in the content. |
Share and Cite
Yang, H.; Chang, M.; Wu, C. Continuous Casting Preparation Process of Helical Fiber-Reinforced Metal Matrix Composites. Metals 2024 , 14 , 832. https://doi.org/10.3390/met14070832
Yang H, Chang M, Wu C. Continuous Casting Preparation Process of Helical Fiber-Reinforced Metal Matrix Composites. Metals . 2024; 14(7):832. https://doi.org/10.3390/met14070832
Yang, Hui, Ming Chang, and Chunjing Wu. 2024. "Continuous Casting Preparation Process of Helical Fiber-Reinforced Metal Matrix Composites" Metals 14, no. 7: 832. https://doi.org/10.3390/met14070832
Article Metrics
Article access statistics, further information, mdpi initiatives, follow mdpi.
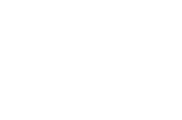
Subscribe to receive issue release notifications and newsletters from MDPI journals
Academia.edu no longer supports Internet Explorer.
To browse Academia.edu and the wider internet faster and more securely, please take a few seconds to upgrade your browser .
Enter the email address you signed up with and we'll email you a reset link.
- We're Hiring!
- Help Center
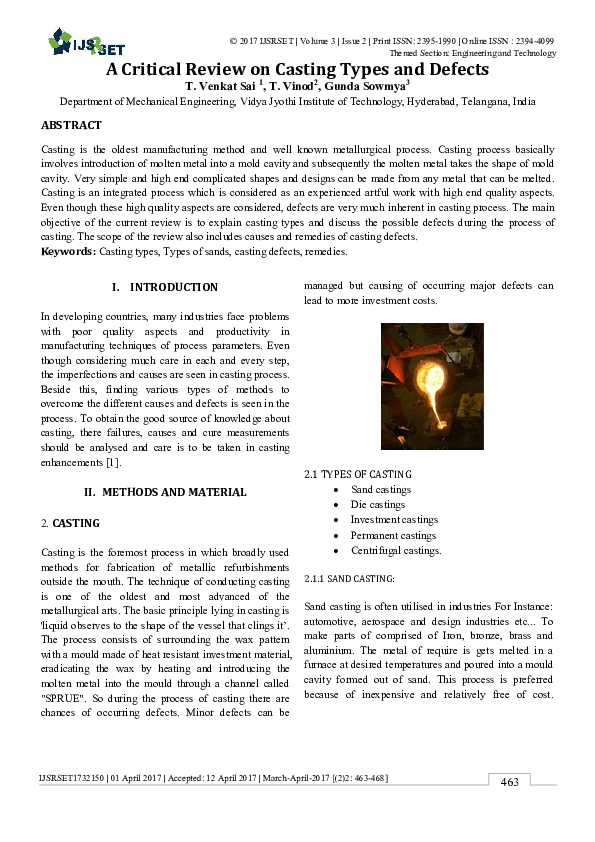
A Critical Review on Casting Types and Defects

Casting is the oldest manufacturing method and well known metallurgical process. Casting process basically involves introduction of molten metal into a mold cavity and subsequently the molten metal takes the shape of mold cavity. Very simple and high end complicated shapes and designs can be made from any metal that can be melted. Casting is an integrated process which is considered as an experienced artful work with high end quality aspects. Even though these high quality aspects are considered, defects are very much inherent in casting process. The main objective of the current review is to explain casting types and discuss the possible defects during the process of casting. The scope of the review also includes causes and remedies of casting defects.
Related Papers
IJAR Indexing
Casting is the one of the oldest manufacturing processes, and even today is the first step in manufacturing most product. In this process the material is first liquefied by proper heating and then this liquefied is poured into a previously prepared mould cavity where it is allowed to solidify and subsequently the product is taken out, cleaned and trimmed to the required shape. During this process there are different critical factors which is contributing in large amount to the defects. These factors are: 1. Design of casting and pattern 2. Moulding sand and design of mould and core. 3. Metal composition. 4. Melting and pouring. 5. Gating system.
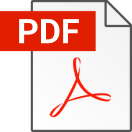
SUPRIYA PRIYADARSINI
Now a day's casting plays a key role for manufacturing industries so its performance should be highly effective in terms of production with minimum number of rejections. So casting yield should be high which can be achieved in highly controlled environment where defects can be minimised so as to minimise the rejections. The challenges of casting defects are to be identified and minimised for effective castings. This paper aims to analyse the causes of different types of defects and provides the remedial measures which will be helpful in improving the quality of product along with increase the productivity. This paper enlists various defects in casting and provides the causes of their occurrence, which will help to analyse the undesirable defects in casting.
IAEME Publication
Casting process is associated with some casting defects that degrade the quality of foundry product. To upgrade the productivity of the organization the casting defects should be minimized. This paper shows the different literature review and root causes of casting defects taken by the different foundry expert's.
IJERA Journal , Madhukar Sorte , Vaibhav Ingle
Many industry aims to improve quality as well as productivity of manufacturing product. So need to number of process parameter to must controlled while casting process, so there are no of uncertainty and defects are face by organizations. In casting process industries are need to technical solution to minimize the uncertainty and defects. In this review paper to represent various casting defects and root causes for engine parts while casting process. Also provide preventive action to improve quality as well as productivity an industrial level.
IAEME PUBLICATION
Global buyers demand defect-free castings and strict delivery schedule, which foundries are finding it verydifficult to meet. Metal casting industry suffers from poor quality and productivity due to the large number of process parameters, combined with lower penetration of manufacturing automation. Casting process involves complex interactions among various parameters and operations related to metal composition, methods design, molding, melting, pouring, shake-out, fettling and machining. For example, if shrinkage porosity is identified as gas porosity, and the pouring temperature is lowered to reduce the same, it may lead to another defect, namely cold shut. Casting defects result in increased unit cost and lower morale of shop floor personnel.Casting defect analysis has been carried out using techniques like cause-effect diagrams, design of experiments, if-then rules (expert systems), and artificial neural networks. Most of the previous work is focused on finding process-related causes for individual defects, and optimizing the parameter values to reduce the defects.The defects are classified in terms of their appearance, size, location, consistency, discovery stage and inspection method. This helps in correct identification of the defects. For defect analysis, the possible causes are grouped into design, material and process parameters. The effect of suspected cause parameters on casting quality is ascertained through simulation. Based on the results and their interpretation, the optimal values of the parameters are determined to eliminate the defects. An integrated understanding of heat transfer during solidification, friction/lubrication at solid–liquid interface, high temperature properties of the solidifying shell etc. is necessary to control the casting process.The influence of steel chemistry on solidification dynamics, particularly with respect to mode of solidification and its consequence on strength and ductility of the solidifying shell, has been dealt with in detail. The application of these basic principles for casting of stainless steel slabs and processing to obtain good quality products has been covered. Castings can unfortunately also sometimes contain other types of defects, such as inclusions of slag or moulding sand, but these are not classified as solidification defects.
Revue des composites et des matériaux avancés
Peter Ikubanni
More reliable and durable parts with high structural integrity are required to meet the increasing advancements in science and technology. This paper reviews five (5) different casting techniques: squeeze casting, sand casting, investment casting, die casting, and continuous casting. Their respective cast products were examined, and their various mechanical properties were discussed. However, these different casting techniques involve a similar fundamental procedure: melting metal, pouring it into a mold, and allowing it to solidify. However, they vary in their physical and mechanical properties, durability, and surface finishing, making one technique more desirable than the other in their application areas. Some techniques were found to be more advantageous and effective than the other, which will aid foundrymen in making the best decision in choosing a technique, considering parameters such as environmental friendliness and cost implications. The appropriate implementation of thes...
Mohammed Ismail
An attempt has been made to describe the casting metallic mold in brief and review the major casting process based on a set of criteria such as step involved, process conceptualization, advantages, disadvantages, and their applications. In addition, the most defects of the casting process are also presented in this study. Based on this review, it can be observed that numerous casting methods are founded and the selection of a process is depend on several factors such as the quality of the casting surface, dimension accuracy, rate production, shape complexity and cost .etc.
International Journal of Scientific Research in Science, Engineering and Technology IJSRSET
Casting process is the most widely used process in manufacturing industries. Production of casting involves various processes like pattern making, molding, and core making and melting. It is very difficult to produce defect free castings. Systematic analysis and identification of sources of product defects are essential for successful manufacturing. Since the quality of casting parts are mostly influenced by process conditions, how to determine the optimum process condition becomes the key to improving part quality. The industry generally tries to eliminate the defects by trial and error method. This paper describes the identification and analysis of the casting defects. Filling related defects, Shape related defects and Thermal related defects of casting products are discussed in this paper. Defects occurred by various gating system parameters are also be identified. So good gating system reduces the defects.
Gourav Vivek Kulkarni
Gourav Kulkarni
In recent times, with the constant utilization of natural resources, every manufacturing unit is turning towards a lean approach. Foundries are no exception to this. Although the fundamental responsibility of a foundry is simply to convert raw metal into a useful casting, it is imperative on their part that the output confirms with the quality as desired and is free from defects of any kind. However, there may be factors like the rate of cooling of molten metal being poured, mould properties, metallurgy of the molten metal being poured and the mould geometry and rigidity to name a few which may have their influence on the casting quality and the overall productivity of the foundry. While striking a balance between the quality and productivity, there may be certain deviations undertaken from the regular course that may lead to casting defects. This paper intends to highlight such interdependencies and suggest indirectly the most feasible means to control casting defects in order to ensure attainment of both quality and productivity. Casting defects considered for this work shall be those observed at a major scale and those which require adequate attention on account of frequency of occurrence. A conclusion shall be drawn towards the end dictating the major findings of the study.
Scientific Bulletin of Valahia University - Materials and Mechanics
Otilia Rusanescu
The paper presents the study of internal defects resulting from the continuous casting of steels. The 50 samples were taken from a total of 20 continuously cast bits of different steel grades. The investigation of the causes of internal defects, shown on the analyzed samples, started from the assumption that the secondary metallurgy was performed correctly. The following internal defects have been evident: internal cracks (axial cracks, section cracks), central porosity and marginal punctuation impurities.
Loading Preview
Sorry, preview is currently unavailable. You can download the paper by clicking the button above.
RELATED PAPERS
IRJET Journal
International Journal of Engineering Research and
veena metri
ATUL BHUJUGADE
Nageswara Posinasetti
Materials Science. Non-Equilibrium Phase Transformations.
Sveto T Cvetkovski
Dr. Ratnakar R . Ghorpade
sreetharan sivam
International Journal of Innovations in Engineering and Science, ISSN:2456-3463 IJIES
Haider Hussain
Marianna Bartošová
Mohamed Abou Omar
International Journal of Engineering Research and Technology (IJERT)
IJERT Journal
IFAC Proceedings Volumes
Petrus Pistorius
International Organization of Scientific Research
Avinash Juriani
Neil Carlson
Archives of Foundry Engineering
Andrzej Trytek
Shrikant Gunjal
Anupinder Singh
IOSR Journal of Engineering
Achamyeleh Kassie
azamar martinez
Dalgobind Mahto
2008 Annual Conference & Exposition Proceedings
Rogelio Luck
IJSTE - International Journal of Science Technology and Engineering
RELATED TOPICS
- We're Hiring!
- Help Center
- Find new research papers in:
- Health Sciences
- Earth Sciences
- Cognitive Science
- Mathematics
- Computer Science
- Academia ©2024
Influence of Casting Materials on the Microstructure and Mechanical Properties of Gray Cast Iron for Cylinder Liners
- Technical Paper
- Published: 24 July 2024
Cite this article
- Shouquan Du ORCID: orcid.org/0009-0004-1551-9507 1 ,
- Chaoyang Chen 2 ,
- Ruirun Chen 1 , 2 ,
- Qi Wang 2 ,
- Xiangyin Cui 1 &
- Qiang Song 1
20 Accesses
Explore all metrics
In this paper, four different casting materials were used to get gray cast iron samples, the effects of different cooling rates caused by different casting materials on graphite distribution, matrix structure and mechanical properties were investigated. The experimental results show that as the cooling rate increases, the graphite form of gray cast iron changed from coarse flake A-type graphite to rosette shaped B-type graphite, graphite increased in quantity and was more evenly distributed. The interlayer spacing of pearlite in matrix decreased with the increase of cooling rate, four different mold casting of cast iron material sample of pearlite lamellar spacing is CO 2 sodium silicate bonded sand mold, 340 nm, oxide ceramic mold, 275 nm, cast iron mold, 141 nm, graphite casting mold, 135 nm, respectively. The reduction of the interlayer spacing of pearlite also significantly improves the tensile strength, compressive strength and hardness. The tensile strength of cast iron specimens cast in graphite casting molds is the highest, at 421 MPa, while the tensile strength of cast iron specimens cast in CO 2 sodium silicate bonded sand molds is the lowest, at 346 MPa. The graphite cast iron sample has the highest compressive strength of 2165 MPa, and the oxide ceramic cast iron sample has the lowest compressive strength of 1115 MPa. The Brinell hardness of the samples cast in cast iron molds is the highest, at 409 HB, while the samples cast in CO 2 sodium silicate bonded sand molds have the lowest Brinell hardness, at 255 HB. In addition, increasing the cooling rate inhibited the diffusion of elements in the melt, reduced the final solidification interval and also reduced the shrinkage porosity and other defects. Fracture analysis shows that cleavage fracture is the main fracture mode of castings. The higher the cooling rate, the smoother the fracture morphology.
This is a preview of subscription content, log in via an institution to check access.
Access this article
Subscribe and save.
- Get 10 units per month
- Download Article/Chapter or eBook
- 1 Unit = 1 Article or 1 Chapter
- Cancel anytime
Price includes VAT (Russian Federation)
Instant access to the full article PDF.
Rent this article via DeepDyve
Institutional subscriptions
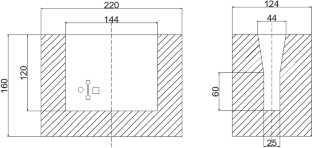
H. Yang, T. Zhou, Q. Wang et al., Effects of laser melting distribution on wear resistance and fatigue resistance of gray cast iron. Metals (2020). https://doi.org/10.3390/met10091257
Article Google Scholar
T.J. Mackin, S.C. Noe, Thermal cracking in disc brakes. Eng. Fail. Anal. 9 (1), 63–76 (2002). https://doi.org/10.1016/S1350-6307(00)00037-6
R. El Soeudy, The effect of graphite aspect ratio on the mechanical and microstructural properties of cast iron. Materialwiss. Werkstofftech. 33 , 73–79 (2002). https://doi.org/10.1002/1521-4052(200202)33:23.0.CO;2-D
L. Collini, G. Nicoletto, R. Konečná, Microstructure and mechanical properties of pearlitic gray cast iron. Mater. Sci. Eng. A 488 (1), 529–539 (2008). https://doi.org/10.1016/j.msea.2007.11.070
Article CAS Google Scholar
M. Moonesan, A. Honarbakhsh raouf, F. Madah, A. Habibollah zadeh et al., Effect of alloying elements on thermal shock resistance of gray cast iron. J. Alloy. Compd. 520 , 226–231 (2012). https://doi.org/10.1016/j.jallcom.2012.01.027
Y.-L. Li, Q. Wang, R.-R. Chen et al., Influence of V content on microstructure and mechanical properties of gray cast iron for super-large cylinder liner. Int. Metalcast. 17 (3), 1806–1814 (2022). https://doi.org/10.1007/s40962-022-00894-7
Z. Li, R. Chen, Q. Wang et al., Effect of Nb addition on compact microstructure and mechanical properties of gray cast iron for cylinder liner. Int. Metalcast (2024). https://doi.org/10.1007/s40962-024-01292-x
A. Hassani, A. Habibollahzadeh, S. Sadeghinejad, Influence of vanadium and chromium additions on the wear resistance of a gray cast iron. Int. J. Miner. Metall. Mater. 19 (7), 602–607 (2012). https://doi.org/10.1007/s12613-012-0601-7
J. Miao, T. Guo, J. Ren et al., Optimization of mechanical and tribological properties of FCC CrCoNi multi-principal element alloy with Mo addition. Vacuum 149 , 324–330 (2018). https://doi.org/10.1016/j.vacuum.2018.01.012
W. Zhai, L. Bai, R. Zhou et al., Recent progress on wear-resistant materials: designs, properties, and applications. Adv. Sci. (2021). https://doi.org/10.1002/advs.202003739
J.F. Janowak, R.B. Gundlach, A Modern Approach to Alloying Gray Iron, (1982)
R.A. Gonzaga, J.F. Carrasquilla, Influence of an appropriate balance of the alloying elements on microstructure and on mechanical properties of nodular cast iron. J. Mater. Process. Technol. 162 , 293–297 (2005). https://doi.org/10.1016/j.jmatprotec.2005.02.040
K.-A. Jafar, A.-A. Behnam, Influence of mold preheating and silicon content on microstructure and casting properties of ductile iron in permanent mold. J. Iron. Steel Res. Int. 18 (3), 34–39 (2011). https://doi.org/10.1016/S1006-706X(11)60034-4
S. Köse, M. Çolak, E.E. Şüküroğlu, Investigation of the effects of filling speed, casting temperature and metallurgical quality on fluidity of lamellar graphite cast iron at different section thicknesses. Int. Metalcast. (2024). https://doi.org/10.1007/s40962-024-01301-z
G. Wu, J. Zhao, Y. Peng, X. Tao, Y. Liu, Effect of pouring temperature on microstructure, tensile properties and hot-tearing susceptibility of a Die-Cast Al–Zn–Mg–Cu Alloy. Int. Metalcast. 17 (1), 455–465 (2022). https://doi.org/10.1007/s40962-022-00782-0
J. Hemanth, K.V.S. Rao, Effect of cooling rate on eutectic cell count, grain size, microstructure, and ultimate tensile strength of hypoeutectic cast iron. J. Mater. Eng. Perform. 8 (4), 417–423 (1999). https://doi.org/10.1361/105994999770346701
O.R. Oloyede, T. Bigg, A.M. Mullis, Effect of Cooling Rate on Drop-Tube Processed Commercial Grey Cast Iron, ASME 2015 International Mechanical Engineering Congress and Exposition, (2015)
V. Fourlakidis, A. Diószegi, A generic model to predict the ultimate tensile strength in pearlitic lamellar graphite iron. Mater. Sci. Eng. A 618 , 161–167 (2014). https://doi.org/10.1016/j.msea.2014.08.061
A. Muumbo, M. Takita, H. Nomura, Processing of semisolid gray cast iron using the cooling plate technique. Mater. Trans. 44 , 893–900 (2003). https://doi.org/10.2320/matertrans.44.893
B. Liu, J. Kang, X. Yang et al., Effects of hollow sand mold on the microstructure and mechanical properties of a low pressure aluminum alloy casting. J. Mater. Res. Technol-JMRT 28 , 4488–4497 (2024). https://doi.org/10.1016/j.jmrt.2023.12.270
J.-L. Li, R.-S. Chen, W. Ke, Microstructure and mechanical properties of Mg-Gd-Y-Zr alloy cast by metal mould and lost foam casting. Trans. Nonferrous Met. Soc. China 21 (4), 761–766 (2011). https://doi.org/10.1016/s1003-6326(11)60777-2
W.A. Ayoola, S.O. Adeosun, O.S. Sanni et al., Effect of casting mould on mechanical properties of 6063 aluminum alloy. J. Eng. Sci. Technol. 7 (1), 89–96 (2012)
Google Scholar
Z. Zhou, Q. Wang, R. Chen et al., Effect of Re addition on microstructure and mechanical properties of Nb-Si-Ti-Al-Cr-Hf ultrahigh temperature alloys. Int. J. Refract. Met. Hard Mat. (2022). https://doi.org/10.1016/j.ijrmhm.2022.105835
A. Holst, A. Buchwalder, P. Hollmann et al., Influence of cooling rate on the microstructural features of a remelted white-solidified cast iron surface and its effects on nitriding behaviour. J. Mater. Process. Technol. 271 , 377–383 (2019). https://doi.org/10.1016/j.jmatprotec.2019.04.004
M.B. Karamış, K. Yıldızlı, Surface modification of nodular cast iron: a comparative study on graphite elimination. Mater. Sci. Eng. A 527 (20), 5225–5229 (2010). https://doi.org/10.1016/j.msea.2010.04.067
N. Zárubová, V. Kraus, J. Čermák, Mechanisms of phase transformations during laser treatment of grey cast iron. J. Mater. Sci. 27 (13), 3487–3496 (1992). https://doi.org/10.1007/BF01151824
B.T. Xiao, Z.T. Fan, X.W. Liu, Grain refinement and hardness of grey cast iron in lost foam casting with mechanical vibration. Metal. Int. 18 (3), 16–18 (2013). https://doi.org/10.1111/j.1475-4959.2011.00424.x
H.R. Abbasi, M. Bazdar, A. Halvaee, Effect of phosphorus as an alloying element on microstructure and mechanical properties of pearlitic gray cast iron. Mater. Sci. Eng. A 444 (1), 314–317 (2007). https://doi.org/10.1016/j.msea.2006.08.108
Download references
Acknowledgments
This work was supported by the National Natural Science Foundation of China (Nos. 52425401 and 52374384), Foundation of National Key Laboratory for Precision Hot Processing of Metals (JCKYS2021603C001).
Author information
Authors and affiliations.
School of Materials Science and Engineering, Shandong University of Science and Technology, Qingdao, 266500, People’s Republic of China
Shouquan Du, Ruirun Chen, Xiangyin Cui & Qiang Song
National Key Laboratory for Precision Hot Processing of Metals, School of Materials Science and Engineering, Harbin Institute of Technology, Harbin, 150001, People’s Republic of China
Chaoyang Chen, Ruirun Chen & Qi Wang
You can also search for this author in PubMed Google Scholar
Corresponding authors
Correspondence to Ruirun Chen or Qi Wang .
Additional information
Publisher's note.
Springer Nature remains neutral with regard to jurisdictional claims in published maps and institutional affiliations.
Rights and permissions
Springer Nature or its licensor (e.g. a society or other partner) holds exclusive rights to this article under a publishing agreement with the author(s) or other rightsholder(s); author self-archiving of the accepted manuscript version of this article is solely governed by the terms of such publishing agreement and applicable law.
Reprints and permissions

About this article
Du, S., Chen, C., Chen, R. et al. Influence of Casting Materials on the Microstructure and Mechanical Properties of Gray Cast Iron for Cylinder Liners. Inter Metalcast (2024). https://doi.org/10.1007/s40962-024-01413-6
Download citation
Received : 19 April 2024
Accepted : 08 July 2024
Published : 24 July 2024
DOI : https://doi.org/10.1007/s40962-024-01413-6
Share this article
Anyone you share the following link with will be able to read this content:
Sorry, a shareable link is not currently available for this article.
Provided by the Springer Nature SharedIt content-sharing initiative
- gray cast iron
- cooling rates
- casting materials
- Find a journal
- Publish with us
- Track your research
- DOI: 10.1016/j.applthermaleng.2024.124005
- Corpus ID: 271342408
Research on temperature field and thermal deformation characteristics of casting rollers in twin-roll casting process
- Yansheng Zhang , Zhen-lei Li , +3 authors Guo-dong Wang
- Published in Applied Thermal Engineering 1 July 2024
- Engineering, Materials Science
38 References
Effect of roll diameter on temperature of aluminum alloy strip during casting using a vertical type high speed twin roll caster, effect of roll material on strip solidification between the rolls of a vertical-type high-speed twin-roll caster, modeling effect of cooling conditions on solidification process during thermal cycle of rollers in twin-roll strip casting, the effect of the thermal deformation of casting roll on strip thickness in the strip casting process, effect of cast roll sleeve material on temperature field of sandwich composite plate solid-liquid-solid twin-roll casting process, research methods and influencing factors of interfacial heat transfer during sub-rapid solidification process of strip casting, formation of deposited oxide film during the sub-rapid solidification of silicon steel droplet and its effect on interfacial heat transfer behavior, air gap measurement during steel-ingot casting and its effect on interfacial heat transfer, two-phase viscoplastic model for the simulation of twin roll casting, near net shape casting: is it possible to cast too thin, related papers.
Showing 1 through 3 of 0 Related Papers
Suggestions or feedback?
MIT News | Massachusetts Institute of Technology
- Machine learning
- Sustainability
- Black holes
- Classes and programs
Departments
- Aeronautics and Astronautics
- Brain and Cognitive Sciences
- Architecture
- Political Science
- Mechanical Engineering
Centers, Labs, & Programs
- Abdul Latif Jameel Poverty Action Lab (J-PAL)
- Picower Institute for Learning and Memory
- Lincoln Laboratory
- School of Architecture + Planning
- School of Engineering
- School of Humanities, Arts, and Social Sciences
- Sloan School of Management
- School of Science
- MIT Schwarzman College of Computing
Machine learning unlocks secrets to advanced alloys
Press contact :.
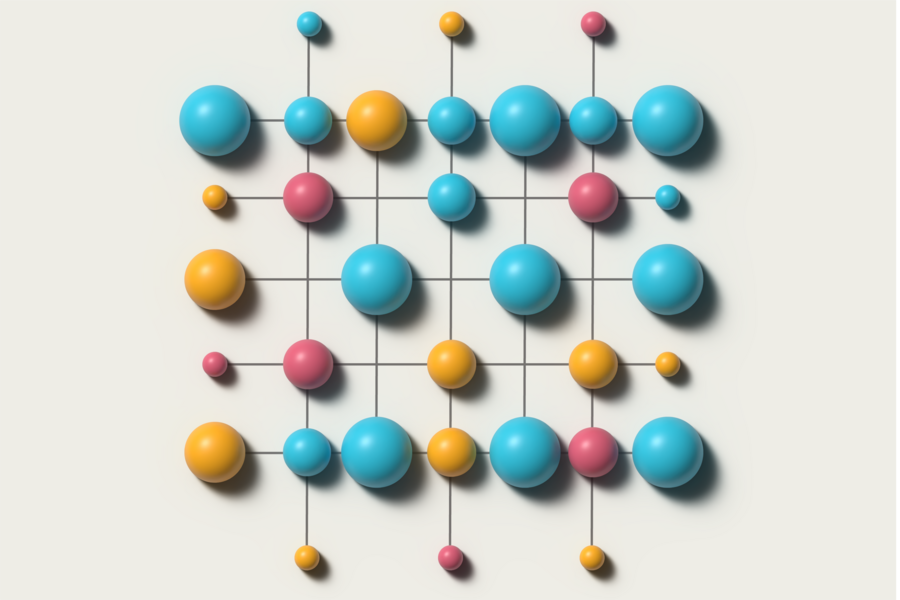
Previous image Next image
The concept of short-range order (SRO) — the arrangement of atoms over small distances — in metallic alloys has been underexplored in materials science and engineering. But the past decade has seen renewed interest in quantifying it, since decoding SRO is a crucial step toward developing tailored high-performing alloys, such as stronger or heat-resistant materials.
Understanding how atoms arrange themselves is no easy task and must be verified using intensive lab experiments or computer simulations based on imperfect models. These hurdles have made it difficult to fully explore SRO in metallic alloys.
But Killian Sheriff and Yifan Cao, graduate students in MIT’s Department of Materials Science and Engineering (DMSE), are using machine learning to quantify, atom-by-atom, the complex chemical arrangements that make up SRO. Under the supervision of Assistant Professor Rodrigo Freitas, and with the help of Assistant Professor Tess Smidt in the Department of Electrical Engineering and Computer Science, their work was recently published in The Proceedings of the National Academy of Sciences .
Interest in understanding SRO is linked to the excitement around advanced materials called high-entropy alloys, whose complex compositions give them superior properties.
Typically, materials scientists develop alloys by using one element as a base and adding small quantities of other elements to enhance specific properties. The addition of chromium to nickel, for example, makes the resulting metal more resistant to corrosion.
Unlike most traditional alloys, high-entropy alloys have several elements, from three up to 20, in nearly equal proportions. This offers a vast design space. “It’s like you’re making a recipe with a lot more ingredients,” says Cao.
The goal is to use SRO as a “knob” to tailor material properties by mixing chemical elements in high-entropy alloys in unique ways. This approach has potential applications in industries such as aerospace, biomedicine, and electronics, driving the need to explore permutations and combinations of elements, Cao says.
Capturing short-range order
Short-range order refers to the tendency of atoms to form chemical arrangements with specific neighboring atoms. While a superficial look at an alloy’s elemental distribution might indicate that its constituent elements are randomly arranged, it is often not so. “Atoms have a preference for having specific neighboring atoms arranged in particular patterns,” Freitas says. “How often these patterns arise and how they are distributed in space is what defines SRO.”
Understanding SRO unlocks the keys to the kingdom of high-entropy materials. Unfortunately, not much is known about SRO in high-entropy alloys. “It’s like we’re trying to build a huge Lego model without knowing what’s the smallest piece of Lego that you can have,” says Sheriff.
Traditional methods for understanding SRO involve small computational models, or simulations with a limited number of atoms, providing an incomplete picture of complex material systems. “High-entropy materials are chemically complex — you can’t simulate them well with just a few atoms; you really need to go a few length scales above that to capture the material accurately,” Sheriff says. “Otherwise, it’s like trying to understand your family tree without knowing one of the parents.”
SRO has also been calculated by using basic mathematics, counting immediate neighbors for a few atoms and computing what that distribution might look like on average. Despite its popularity, the approach has limitations, as it offers an incomplete picture of SRO.
Fortunately, researchers are leveraging machine learning to overcome the shortcomings of traditional approaches for capturing and quantifying SRO.
Hyunseok Oh , assistant professor in the Department of Materials Science and Engineering at the University of Wisconsin at Madison and a former DMSE postdoc, is excited about investigating SRO more fully. Oh, who was not involved in this study, explores how to leverage alloy composition, processing methods, and their relationship to SRO to design better alloys. “The physics of alloys and the atomistic origin of their properties depend on short-range ordering, but the accurate calculation of short-range ordering has been almost impossible,” says Oh.
A two-pronged machine learning solution
To study SRO using machine learning, it helps to picture the crystal structure in high-entropy alloys as a connect-the-dots game in an coloring book, Cao says.
“You need to know the rules for connecting the dots to see the pattern.” And you need to capture the atomic interactions with a simulation that is big enough to fit the entire pattern.
First, understanding the rules meant reproducing the chemical bonds in high-entropy alloys. “There are small energy differences in chemical patterns that lead to differences in short-range order, and we didn’t have a good model to do that,” Freitas says. The model the team developed is the first building block in accurately quantifying SRO.
The second part of the challenge, ensuring that researchers get the whole picture, was more complex. High-entropy alloys can exhibit billions of chemical “motifs,” combinations of arrangements of atoms. Identifying these motifs from simulation data is difficult because they can appear in symmetrically equivalent forms — rotated, mirrored, or inverted. At first glance, they may look different but still contain the same chemical bonds.
The team solved this problem by employing 3D Euclidean neural networks . These advanced computational models allowed the researchers to identify chemical motifs from simulations of high-entropy materials with unprecedented detail, examining them atom-by-atom.
The final task was to quantify the SRO. Freitas used machine learning to evaluate the different chemical motifs and tag each with a number. When researchers want to quantify the SRO for a new material, they run it by the model, which sorts it in its database and spits out an answer.
The team also invested additional effort in making their motif identification framework more accessible. “We have this sheet of all possible permutations of [SRO] already set up, and we know what number each of them got through this machine learning process,” Freitas says. “So later, as we run into simulations, we can sort them out to tell us what that new SRO will look like.” The neural network easily recognizes symmetry operations and tags equivalent structures with the same number.
“If you had to compile all the symmetries yourself, it’s a lot of work. Machine learning organized this for us really quickly and in a way that was cheap enough that we could apply it in practice,” Freitas says.
Enter the world’s fastest supercomputer
This summer, Cao and Sheriff and team will have a chance to explore how SRO can change under routine metal processing conditions, like casting and cold-rolling, through the U.S. Department of Energy’s INCITE program , which allows access to Frontier , the world’s fastest supercomputer.
“If you want to know how short-range order changes during the actual manufacturing of metals, you need to have a very good model and a very large simulation,” Freitas says. The team already has a strong model; it will now leverage INCITE’s computing facilities for the robust simulations required.
“With that we expect to uncover the sort of mechanisms that metallurgists could employ to engineer alloys with pre-determined SRO,” Freitas adds.
Sheriff is excited about the research’s many promises. One is the 3D information that can be obtained about chemical SRO. Whereas traditional transmission electron microscopes and other methods are limited to two-dimensional data, physical simulations can fill in the dots and give full access to 3D information, Sheriff says.
“We have introduced a framework to start talking about chemical complexity,” Sheriff explains. “Now that we can understand this, there’s a whole body of materials science on classical alloys to develop predictive tools for high-entropy materials.”
That could lead to the purposeful design of new classes of materials instead of simply shooting in the dark.
The research was funded by the MathWorks Ignition Fund, MathWorks Engineering Fellowship Fund, and the Portuguese Foundation for International Cooperation in Science, Technology and Higher Education in the MIT–Portugal Program.
Share this news article on:
Related links.
- Rodrigo Freitas
- INCITE Program
- Department of Materials Science and Engineering
Related Topics
- Materials science and engineering
- Artificial intelligence
- Computer modeling
- Electrical Engineering & Computer Science (eecs)
Related Articles
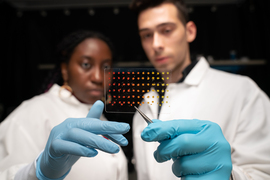
New computer vision method helps speed up screening of electronic materials
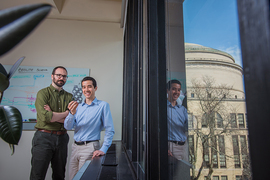
Designing zeolites, porous materials made to trap molecules
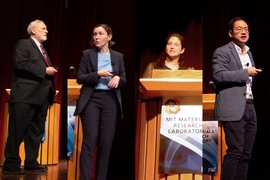
Materials Day talks examine the promises and challenges of AI and machine learning
Previous item Next item
More MIT News

Edgerton Center hosts workshop for deaf high school students in STEM
Read full story →

MIT Global SCALE Network expands by adding center at Loughborough University
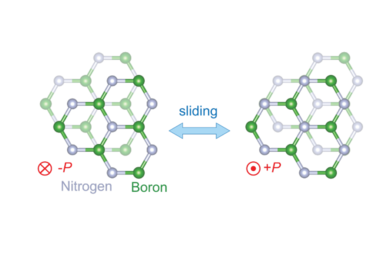
New transistor’s superlative properties could have broad electronics applications
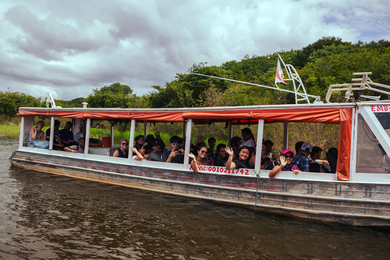
When learning at MIT means studying thousands of miles away
Flying high to enable sustainable delivery, remote care
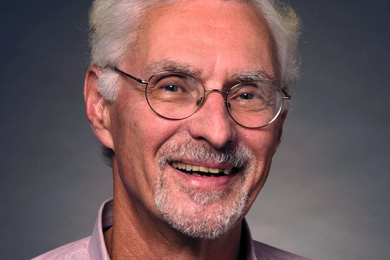
Professor Emeritus Ralph Gakenheimer, mobility planner and champion of international development, dies at 89
- More news on MIT News homepage →
Massachusetts Institute of Technology 77 Massachusetts Avenue, Cambridge, MA, USA
- Map (opens in new window)
- Events (opens in new window)
- People (opens in new window)
- Careers (opens in new window)
- Accessibility
- Social Media Hub
- MIT on Facebook
- MIT on YouTube
- MIT on Instagram
Unfortunately we don't fully support your browser. If you have the option to, please upgrade to a newer version or use Mozilla Firefox , Microsoft Edge , Google Chrome , or Safari 14 or newer. If you are unable to, and need support, please send us your feedback .
We'd appreciate your feedback. Tell us what you think! opens in new tab/window
Sharing research data
As a researcher, you are increasingly encouraged, or even mandated, to make your research data available, accessible, discoverable and usable.
Sharing research data is something we are passionate about too, so we’ve created this short video and written guide to help you get started.
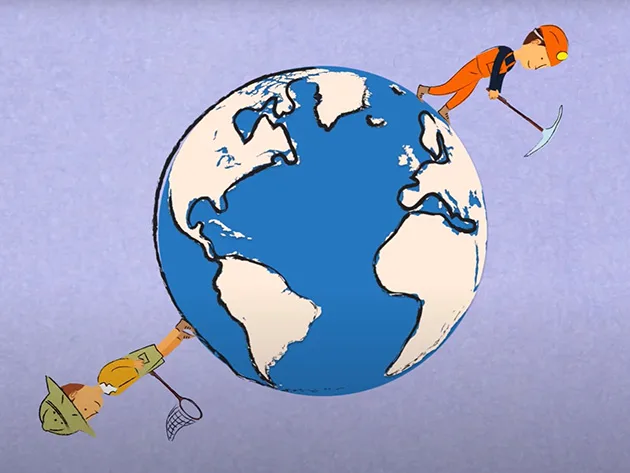
Research Data
What is research data.
While the definition often differs per field, generally, research data refers to the results of observations or experiments that validate your research findings. These span a range of useful materials associated with your research project, including:
Raw or processed data files
Research data does not include text in manuscript or final published article form, or data or other materials submitted and published as part of a journal article.
Why should I share my research data?
There are so many good reasons. We’ve listed just a few:
How you benefit
You get credit for the work you've done
Leads to more citations! 1
Can boost your number of publications
Increases your exposure and may lead to new collaborations
What it means for the research community
It's easy to reuse and reinterpret your data
Duplication of experiments can be avoided
New insights can be gained, sparking new lines of inquiry
Empowers replication
And society at large…
Greater transparency boosts public faith in research
Can play a role in guiding government policy
Improves access to research for those outside health and academia
Benefits the public purse as funding of repeat work is reduced
How do I share my research data?
The good news is it’s easy.
Yet to submit your research article? There are a number of options available. These may vary depending on the journal you have chosen, so be sure to read the Research Data section in its Guide for Authors before you begin.
Already published your research article? No problem – it’s never too late to share the research data associated with it.
Two of the most popular data sharing routes are:
Publishing a research elements article
These brief, peer-reviewed articles complement full research papers and are an easy way to receive proper credit and recognition for the work you have done. Research elements are research outputs that have come about as a result of following the research cycle – this includes things like data, methods and protocols, software, hardware and more.
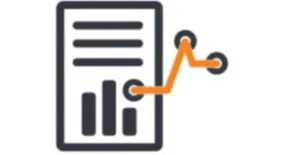
You can publish research elements articles in several different Elsevier journals, including our suite of dedicated Research Elements journals . They are easy to submit, are subject to a peer review process, receive a DOI and are fully citable. They also make your work more sharable, discoverable, comprehensible, reusable and reproducible.
The accompanying raw data can still be placed in a repository of your choice (see below).
Uploading your data to a repository like Mendeley Data
Mendeley Data is a certified, free-to-use repository that hosts open data from all disciplines, whatever its format (e.g. raw and processed data, tables, codes and software). With many Elsevier journals, it’s possible to upload and store your data to Mendeley Data during the manuscript submission process. You can also upload your data directly to the repository. In each case, your data will receive a DOI, making it independently citable and it can be linked to any associated article on ScienceDirect, making it easy for readers to find and reuse.
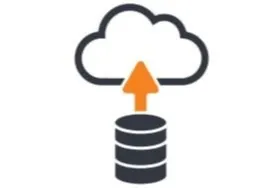
View an article featuring Mendeley data opens in new tab/window (just select the Research Data link in the left-hand bar or scroll down the page).
What if I can’t submit my research data?
Data statements offer transparency.
We understand that there are times when the data is simply not available to post or there are good reasons why it shouldn’t be shared. A number of Elsevier journals encourage authors to submit a data statement alongside their manuscript. This statement allows you to clearly explain the data you’ve used in the article and the reasons why it might not be available. The statement will appear with the article on ScienceDirect.
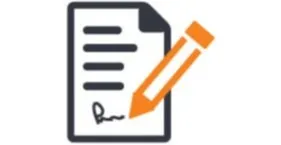
View a sample data statement opens in new tab/window (just select the Research Data link in the left-hand bar or scroll down the page).
Showcasing your research data on ScienceDirect
We have 3 top tips to help you maximize the impact of your data in your article on ScienceDirect.
Link with data repositories
You can create bidirectional links between any data repositories you’ve used to store your data and your online article. If you’ve published a data article, you can link to that too.
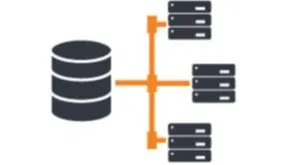
Enrich with interactive data visualizations
The days of being confined to static visuals are over. Our in-article interactive viewers let readers delve into the data with helpful functions such as zoom, configurable display options and full screen mode.
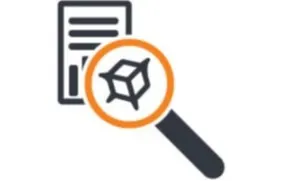
Cite your research data
Get credit for your work by citing your research data in your article and adding a data reference to the reference list. This ensures you are recognized for the data you shared and/or used in your research. Read the References section in your chosen journal’s Guide for Authors for more information.
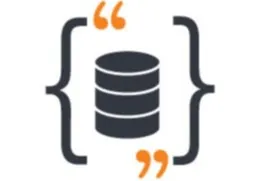
Ready to get started?
If you have yet to publish your research paper, the first step is to find the right journal for your submission and read the Guide for Authors .
Find a journal by matching paper title and abstract of your manuscript in Elsevier's JournalFinder opens in new tab/window
Find journal by title opens in new tab/window
Already published? Just view the options for sharing your research data above.
1 Several studies have now shown that making data available for an article increases article citations.
- Venue: Shaw Centre, Ottawa
- Registration
- Visa and Travel Authorization
- Travelling to Ottawa
- Getting Around Ottawa
- Code of Conduct
- Equity, Diversity, and Inclusion Plan
- Fun Activities
- Sponsorship
- Research and Experience Papers
- Doctoral Symposium
- Industry Talks
- CAIN 2025 Committees
- Organizing Committee
- Steering Committee
- Track Committees
- Contributors
- People Index
Research and Experience Papers CAIN 2025
Call for submissions.
We invite submissions of research and experience papers in two categories:
- Long paper : Long papers are research or experience papers describing research results, case studies, or insights from industry experience. A research or experience full paper is up to 10 pages plus a maximum of 2 pages for references.
- Short paper : Papers describing new challenges, new research results, visionary ideas, or experiences from, or in cooperation with, practitioners are welcome as short papers. In-progress research with interim results is also appropriate for a short paper. A short paper is up to 5 pages plus a maximum of 1 page for references.
The paper submissions will undergo a double-anonymous review process with three independent reviews and a virtual PC discussion. Acceptance criteria include contribution to the field of software engineering for AI, novelty, research and industrial relevance, soundness, and results. The accepted full and short papers will be published in the ICSE Companion proceedings.
If a paper is rejected as a long paper because the reviewers consider that the research is in the early stages or lacking evaluation, the paper will be reevaluated as a short paper. If accepted as a short paper, authors can choose to accept or decline to resubmit as a short paper.
Important Dates
- Abstracts: Nov 19, 2024, AoE (recommended; used for bidding)
- Papers: Nov 26, 2024, AoE (firm; no extensions)
- Notifications: Jan 21, 2025, AoE
- Camera Ready: Feb 12, 2025, AoE
Scope and Topics of Interest
The area of interest for CAIN is Software Engineering for AI — improving the development of AI-based systems throughout the full life cycle. Topics include but are not limited to:
- System and software requirements and their relationship to AI/ML modeling.
- Data management ensuring relevance and efficiency related to business goals.
- System and software architecture for AI-enabled systems.
- Integration of AI and software development processes into the AI system development life cycle, including continuous integration and deployment, and system and software evolution.
- Ensuring and managing system and software nonfunctional properties and their relationship to AI/ML properties, including runtime properties such as performance, safety, security, and reliability; and life-cycle properties including reusability, maintainability and evolution.
- Collaboration, organizational, and management practices for a successful development of AI-enabled systems.
- Building effective infrastructures to support development of AI systems and components.
- Further clarifications on the CAIN Scope
Note: Submissions that report strictly on data science or model development without any connection to software engineering and AI-enabled systems will be desk-rejected. As stated earlier, there are many venues for those papers where authors would get much more valuable and relevant feedback.
Submission Form
Research and experience papers should be submitted to (TBA). The submission deadline is firm, no extensions.
All submissions must adhere to the following requirements:
- Page limit is 10 pages plus 2 additional pages of references for long papers and 5 pages plus 1 additional page for references for short papers.
- Submissions must be unpublished original work and should not be under review or submitted elsewhere while being under consideration.
- By submitting to CAIN, authors acknowledge that they are aware of and agree to be bound by the ACM Policy and Procedures on Plagiarism and IEEE Plagiarism FAQ . The authors also acknowledge that they conform to the authorship policy of the ACM and the authorship policy of the IEEE .
- Authors’ names must be omitted from the submitted paper.
- All references to the author’s prior work should be in the third person.
- Authors are encouraged to title their submission differently than preprints of the authors on ArXiV or similar sites. During review, authors should not publicly use the submission title.
Submissions must conform to the IEEE conference proceedings template, specified in the IEEE Conference Proceedings Formatting Guidelines (title in 24pt font and full text in 10pt type, LaTeX users must use \documentclass[10pt,conference]{IEEEtran} without including the compsoc or compsocconf options).
Accepted papers will be published in the ICSE 2025 Co-located Event Proceedings and included in the IEEE and ACM Digital Libraries. Authors of accepted papers are required to register and present their accepted paper at the conference in order for the paper to be included in the proceedings and the Digital Libraries.
The official publication date is the date the proceedings are made available in the ACM or IEEE Digital Libraries. This date may be up to two weeks prior to the first day of ICSE 2025. The official publication date affects the deadline for any patent filings related to published work.
Authors of papers receiving a Conditional Accept decision are expected to submit the revised papers with changes marked in a different color, such as using LaTeXdiff. The authors also need to submit an “Author Response” document capturing the authors’ response to each reviewer comment and how those comments were addressed in the revision. This is similar to the “Summary of Changes and Response” document that is typically submitted by authors for a journal paper major revision. The reviewers will check the revised paper against the original paper and the suggested changes. Conditional Accepts will be checked by only one member of the Program Committee, and this will be done in one pass.
Authors of rejected long papers may receive an acceptance as a short paper if the PC chairs and reviewers agree that it better meets the criteria for short papers. In this case, authors may decide to accept or reject the invitation if they would rather submit as a long paper to a different venue.
Similarly, authors of rejected long and short papers relevant to the field of AI Engineering may have their papers sent to a different CAIN track. Also in this case, authors may decide to accept or reject the invitation.
Submission Process
Research and experience papers should be submitted to HotCrp (link TBD). The submission deadline is firm, with no extensions.
- Submissions must be in PDF and strictly conform to the IEEE conference proceedings formatting instructions. Alterations of spacing, font size, and other changes that deviate from the instructions may result in desk rejection without further review.
- All submissions must conform to the IEEE conference proceedings template, specified in the IEEE Conference Proceedings Formatting Guidelines (title in 24pt font and full text in 10pt type, LaTeX users must use \documentclass[10pt, conference]{IEEEtran} without including the compsoc or compsocconf options). Submissions must strictly conform to the IEEE conference proceedings formatting instructions specified above. Alterations of spacing, font size, and other changes that deviate from the instructions may result in desk rejection without further review.
- By submitting to CAIN, authors acknowledge that they are aware of and agree to be bound by the ACM Policy and Procedures on Plagiarism and the IEEE Plagiarism FAQ. Papers submitted to CAIN 2025 must not have been published elsewhere and must not be under review or submitted for review elsewhere while under consideration for CAIN 2025. Contravention of this concurrent submission policy will be deemed a serious breach of scientific ethics, and appropriate action will be taken in all such cases. To check for double submission and plagiarism issues, the chairs reserve the right to (1) share the list of submissions with the PC Chairs of other conferences with overlapping review periods and (2) use external plagiarism detection software, under contract to the ACM or IEEE, to detect violations of these policies.
- By submitting to the CAIN, authors acknowledge that they conform to the authorship policy of the ACM, and the authorship policy of the IEEE.
- If the research involves human participants/subjects, the authors must adhere to the ACM Publications Policy on Research Involving Human Participants and Subjects. Upon submitting, authors will declare their compliance with such a policy. Alleged violations of this policy or any ACM Publications Policy will be investigated by ACM and may result in a full retraction of your paper, in addition to other potential penalties, as per ACM Publications Policy.
- Please ensure that you and your co-authors obtain an ORCID ID, so you can complete the publishing process for your accepted paper. ACM and IEEE have been involved in ORCID and may collect ORCID IDs from all published authors. We are committed to improve author discoverability, ensure proper attribution and contribute to ongoing community efforts around name normalization; your ORCID ID will help in these efforts.
- No members yet
- Apply to UMaine
Watershed Process and Estuary Sustainability Research Group
Wpes begins new colorado river sediment mapping project.
The WPES research group has initiated a new collaborative project focused on mapping channel bottom textures in the Colorado River below Glen Canyon Dam. The work uses data acquired by the USGS during previous river measurement expeditions and expands on techniques described by Buscombe, Grams, and Smith (2015) . The research has relevance to river management decision making, coincidently the focus of interviews on PBS News Hour this week that includes WPES colleague, Dr. Jack Schmidt, from Utah State University.
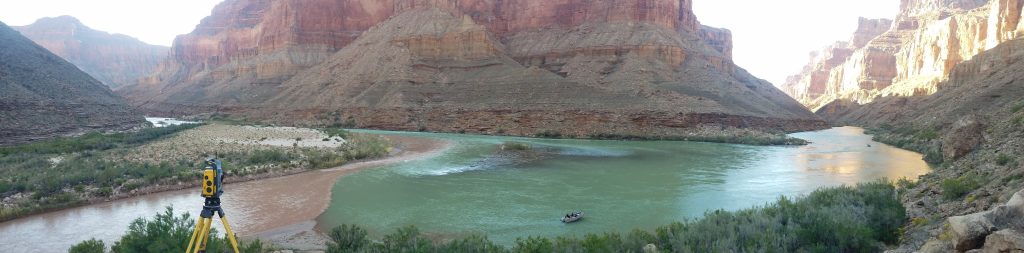
You are using an outdated browser. Please upgrade your browser to improve your experience.

COMMENTS
In this paper the statistical analysis is aimed to optimize process parameters at the case study, i.e. Akaki Basic Metals Industry (ABMI) in Addis Ababa Ethiopia, to minimize major steel casting ...
Abstract: On the way to building smart factories as the vision of Industry 4.0, the casting process. stands out as a specific manufacturing process due to its diversity and complexity. One of the ...
Introduction. Casting is a process in which molten metal flows by gravity or other force into a mold. where it solidifies in the shape of the mold cavity. The term casting also applies to the part ...
The International Journal of Cast Metals Research is devoted to the dissemination of peer reviewed information on the science and engineering of cast metals, solidification and casting processes. Assured production of high integrity castings requires an integrated approach that optimises casting, mould and gating design; mould materials and binders; alloy composition and microstructure; metal ...
On the way to building smart factories as the vision of Industry 4.0, the casting process stands out as a specific manufacturing process due to its diversity and complexity. One of the segments of smart foundry design is the application of artificial intelligence in the improvement of the casting process. This paper presents an overview of the conducted research studies, which deal with the ...
This paper reviews and summarizes the research history and current situation of numerical simulation of casting process. The progress in numerical simulation from five aspects of casting solidification, casting filling, stress field, microstructure, commercial software, is presented.
Continuous casting is a process whereby molten metal is solidified into semi-finished billets, blooms, slabs or strips for subsequent rolling in finishing mills; it is the most frequently used process to cast not only steel, but also aluminum and copper alloys, with the main configurations being as shown in Figure 1.
Casting is a process in which a molten material flows into a mold and is allowed to solidify, taking the shape of the mold. Casting can be done simply (such as gravity-pouring metal into an open mold), or it can be part of a complex process (such as forming a semisolid slurry that is injected into a closed metal mold).
[4] has done a research on minimisation of casting defects by analysing the root causes of some casting defects in ABMI industries. In this paper the statistical analysis is aimed to optimize process parameters at the case study, i.e., Akaki Basic Metals Industry (ABMI) in Addis Ababa Ethiopia, to minimize major steel casting defects.
For the purpose of this paper, process knowledge is defined and understood based on Roshan’s definition. Figure 1 below summarises and illustrates the concept of process knowledge. ... Sand Casting process and sustainability Sand casting also known as sand moulding is a metal manufacturing process categorized by utilizing sand as an ...
Purpose. Casting is one of the well-known manufacturing processes to make durable parts of goods and machinery. However, the quality of the casting parts depends on the proper choice of process variables related to properties of the materials used in making a mold and the product itself; hence, variables related to product/process designs are taken into consideration.
Much research has been carried out on the casting process of the automobile wheel. Zhang et al. [ 1 ] developed a mathematical model of the low-pressure die-casting process for the production of A356 aluminum alloy wheels to predict the evolution of temperature within the wheel and die.
Casting defect analysis is the process of finding root causes of occurrence of defects in the rejection of casting and taking necessary step to reduce the defects and to improve the casting yield. In this review paper an attempt has been made to provide all casting related defect with their causes and remedies.
The casting process was discovered probably around 3500 BC in Mesopotamia. Casting is unique manufacturing processes for a variety of reasons. Perhaps the most obvious is the array of molding and casting processes available that are capable of producing complex components in any metal, ranging in weight from less than an ounce to single parts ...
To improve the strength of the metal while maintaining good plasticity, helical fibers are added to the metal matrix. How to form helical fiber and control its parameters in the preparation process are urgent problems to be solved in the study of helical fiber-reinforced metal matrix composites. In this paper, the continuous casting process of helical fiber-reinforced metal matrix composites ...
Casting defect analysis is the process of finding root causes of occurrence of defects in the rejection of casting and taking necessary step to reduce the defects. A proper methodology is formed consisting of various quality control tools such as Pareto analysis, Ishikawa diagram (cause and effect diagram), brainstorming, why-why analysis.
The present study delves into the intricate domain of advanced casting processes, with a specific emphasis on the areas of design, simulation, and process control.
casting. Casting is the process of filling the liquid metal into a shaped mould to get the desired shape of the product. Filling the mold casting process affects significantly the heat transfer & solidification of the melt. A finite element formulation is to be used for it, which gives temperature profiles at different time steps.
International Journal of Scientific Research in Science, Engineering and Technology (ijsrset.com) 464 However, flaws are very common in sand cast parts and these affects the properties of castings. 2.1.2 DIE CASTING Die casting is a metal casting process that is characterized by forcing molten metal under high pressure into a mold cavity. The mold cavity is created using two hardened tool ...
In this paper, four different casting materials were used to get gray cast iron samples, the effects of different cooling rates caused by different casting materials on graphite distribution, matrix structure and mechanical properties were investigated. The experimental results show that as the cooling rate increases, the graphite form of gray cast iron changed from coarse flake A-type ...
The objective of the paper is provide a comparative study of mold fabrication between traditional sand casting process and new developed 3D printing process. This paper is arranged as follows. In Section 2, the process of 3D printed moldand core will be prese nted due to its uniqueness, followed by assembly of the mold components.
International Research Journal of Engineering and Technology (IRJET) e-ISSN: 2395-0056 Volume: 09 Issue: 07 | July 2022 www.irjet.net p-ISSN: 2395-0072 ... centrifugal casting process studied based on results of complete simulation. Rupesh Kumar Verma Manoj Chocolate [3] This paper delivers a review of the influence of material and process ...
DOI: 10.1016/j.applthermaleng.2024.124005 Corpus ID: 271342408; Research on temperature field and thermal deformation characteristics of casting rollers in twin-roll casting process
Sheriff is excited about the research's many promises. One is the 3D information that can be obtained about chemical SRO. Whereas traditional transmission electron microscopes and other methods are limited to two-dimensional data, physical simulations can fill in the dots and give full access to 3D information, Sheriff says.
These brief, peer-reviewed articles complement full research papers and are an easy way to receive proper credit and recognition for the work you have done. Research elements are research outputs that have come about as a result of following the research cycle - this includes things like data, methods and protocols, software, hardware and more.
A case study detailing concentrations and chemical compositions of microplastic fibers in Frenchman Bay and its upstream estuaries and rivers has been published in the journal Environmental Engineering Science. The paper, Land-Sea Connection of Microplastic Fiber Pollution in Frenchman Bay, Maine, reveals that as many as 400 billion microplastic fibers may be found in the […]
48. Quality improvement of a casting process using design of experiments. 1.INTRODUCTION. Most of the pumping and allied components in today's. world are produced by metal casting. Sand casting ...
Call for Submissions We invite submissions of research and experience papers in two categories: Long paper: Long papers are research or experience papers describing research results, case studies, or insights from industry experience. A research or experience full paper is up to 10 pages plus a maximum of 2 pages for references. Short paper: Papers describing new challenges, new research ...
The WPES research group has initiated a new collaborative project focused on mapping channel bottom textures in the Colorado River below Glen Canyon Dam. The work uses data acquired by the USGS during previous river measurement expeditions and expands on techniques described by Buscombe, Grams, and Smith (2015). The research has relevance to river management […]
Turkiye's defence industry has undergone dramatic changes over the last 50 years and the country has become a significant defence exporter. In this report, as part of a joint project with the IISS, researchers from the Center for Foreign Policy and Peace Research explore this process and the issues lying ahead.